17 Risk assessment process: Uncertainty in controls
17.1 Chapter overview
Cross reference to ISO31000 Clause 6.3 and ISO45001 clauses 6.1 and 8.1.
Check for key readings, webinars, and videos for complementary resources.
Definitions of italicised terms are in the Glossary.
Relevant law
- Health and Safety at Work Act 2015
- Health and Safety at Work (General Risk and Workplace Management) Regulations 2016
- Health and Safety at Work (Major Hazard Facilities) Regulations 2016
Key questions
What is or will be the impact of artificial intelligence on the business?
If risk is the “effect of uncertainty on objectives”:
- what are the objectives of the organisation, activity, system, or item?
- how widely should the scope of the assessment be set?
- what uncertainties could affect achievement of those objectives?
Useful management techniques
The following management techniques may help with assessing controls.
- Assurance mapping (see section 21.3.2)
- Controls effectiveness rating (see section 21.3.6)
- Control self-assessment (see section 21.3.7)
- Failure modes, effects, and consequences analysis (see section 21.3.10)
- Interviews (see section 0)
- Layers of protection analysis (see section 21.3.21).
See also section 6.2 for a theoretical discussion of controls as part of a management system.
17.2 What are controls?
A risk control is a “measure that maintains and/or modifies risk” and includes any process, policy, device, practice, or other actions which modify risk. However, controls may not always exert the intended or assumed modifying effect (ISO31000, 2018). We can substitute in the definition of risk to give: “measure that maintains and/or modifies the effect of uncertainty on objectives”.
Review Figure 35, the risk model, to see where controls can modify a wide range of causal and consequence factors. If you have used bow tie analysis you will see where controls are intended to modify risk, or where there are control gaps. Note that risks are maintained or modified rather than just reduced. This allows for treatment of a wider range of causal or consequence factors, and for opportunities that have positive consequences.
Read regulation 7 in the Health and Safety at Work (General Risk and Workplace Management) Regulations 2016 that requires that “A PCBU who implements a control measure to eliminate or minimise risks to health and safety must ensure that the control measure is effective, and is maintained so that it remains effective, including by ensuring that the control measure is, and continues to be:
(a) fit for purpose; and
(b) suitable for the nature and duration of the work; and
(c) installed, set up, and used correctly”.
Regulation 8 then sets out a duty to review control measures. Read this lengthy Regulation and think about when and how it might apply to work carried out in a PCBU you are familiar with.
17.3 Health and safety legislation on controls
Read section 30 of the Health and Safety at Work Act 2015 and then Regulations 3, and 6-8 of the Health and Safety at Work (General Risk and Workplace) Regulations (2016).
These notes explore the hierarchies of control in New Zealand legislation: check for updates. Examples are non-exhaustive illustrations of some possible controls. Some may come under two or more headings. Each requires evaluation for likely effectiveness before implementation. See also the British HSE (2014) guidance document The health and safety toolbox: How to control risks at work.
It is essential to work down the hierarchy of control and only use administrative controls or personal protective equipment if there are no other options.
17.3.1 Plant, equipment and OHS controls
Read the definition of “plant” in the Health and Safety at Work Act 2015. Some things not ordinarily thought off as plant are included in this definition and “plant” should be interpreted widely by a PCBU. Some practicable ways to achieve safe plant are set out below. AS/NZS4024 Safety of machinery was adopted from a multi-part international standard and published by Standards New Zealand. See also Figure 50, the mind map of machinery hazards.
Table 27. How to comply with the legislation – plant
Requirement in the Act and Regulations | What this may require | Examples for safe use of plant |
Eliminating the risk | Change in work activities | Stop use of the plant and remove it from the workplace
Redesign the process or product to eliminate the plant Contract out the process to a PCBU better equipped to carry out the work |
Substituting (wholly or partly) the hazard giving rise to the risk with something that gives rise to a lesser risk | Use safer plant | Replace older plant with inherently safe plant |
Isolating the hazard from any person exposed to it | Enclosure of the plant giving rise to the hazard | Enclose noisy plant |
Preventing any person from coming into contact with the hazard | Barriers in workplaces | Enclose workers in an “acoustic” control room
Safety cage in a deep excavation Edge guards on above-ground construction sites Have markings on automatic glass doors |
Implementing engineering controls | “Guarding” in the broadest sense | Design plant so the hazard is “locked in”, preventing it from escaping and harming workers
Refer AS/NZS4024 for guidance |
Implementing administrative controls | Safe system of work | Restrict use of plant to competent workers who have permission to use it
Operate a permit-to-work system for maintenance access Use standard operating procedures for plant Provide information, training, instruction, supervision |
Ensuring the provision and use of suitable personal protective equipment (PPE) | As a last resort and based on an effective risk assessment, select, and ensure use of correct PPE | In relation to plant, PPE may include hearing protection, eye protection, full face protection; hand protection, full forearm protection |
17.3.2 Structures and OHS controls
Read the definition of “structure” in the Health and Safety at Work Act 2015. Some things not ordinarily thought off as structure are included in this definition and ” structure” should be interpreted widely by a PCBU. Some of the practicable ways to achieve safe plant are set out below.
Table 28. How to comply with the legislation – structures
Requirement in the Act and Regulations | What this may require | Examples for safe use of structures |
Eliminating the risk | Change in work activities | Stop use of the plant or structure and remove it from the workplace
Redesign the process or product Contract out the process to a PCBU better equipped to carry out the work |
Substituting (wholly or partly) the hazard giving rise to the risk with something that gives rise to a lesser risk | Use safer structures | Build “towers” on their side and hoist into vertical when constructed
Replace non-standard elements of a structure with standard (eg, stairs) Use a mobile elevating work platform instead of mobile scaffolding Use tower scaffolding instead of ladders Use mobile elevating work platforms instead of ladders |
Isolating the hazard from any person exposed to it | Enclose the structure giving rise to the hazard | Safety cage or similar support in a deep excavation |
Preventing any person from coming into contact with the hazard | Barriers in workplaces | Use edge guards on above-ground construction sites
Fall protection Have markings on hard-to-see automatic glass doors Use suspended-access cradles on structures to enable safe maintenance Install general ventilation and heating systems |
Implementing engineering controls | Design the structure so the hazard is “locked in”, preventing it from escaping and harming workers | Lock lift and escalator motor rooms
|
Implementing administrative controls | Safe system of work | Restrict use of a structure to competent workers who have permission to use it
Operate a permit-to-work system for maintenance access Provide information, training, instruction, supervision (see Table 31) |
Ensuring the provision and use of suitable personal protective equipment (PPE) | As a last resort and based on an effective risk assessment, select, and ensure use of correct PPE | In relation to structures PPE may include: • eye protection • full face protection • hand protection • full forearm protection |
Health and Safety at Work Act: plant and structures
Some things not ordinarily thought off as plant are included in the definition so “plant” should be interpreted widely by a PCBU. This follows a comment by Munkman (1975, p. 105) that plant is “a convenient general term to denote all manner of things employed in the course of the work”.
Some things that might not be ordinarily thought off as structures are included in the definition in the Act so “structure” should be interpreted widely by a PCBU. There is also some overlap between plant and structures, raising possible compliance issues. For example, does the location or environment of an item change the standard, code or other guidance that should be applied to an item? What qualifications or experience should a worker have before being allowed to work on a specific item?
The Act also defines prescribed high-risk plant to mean:
… plant prescribed by regulations as high-risk plant
It is not uncommon for process plant to be large with structural access in the form of stairs and walkways.
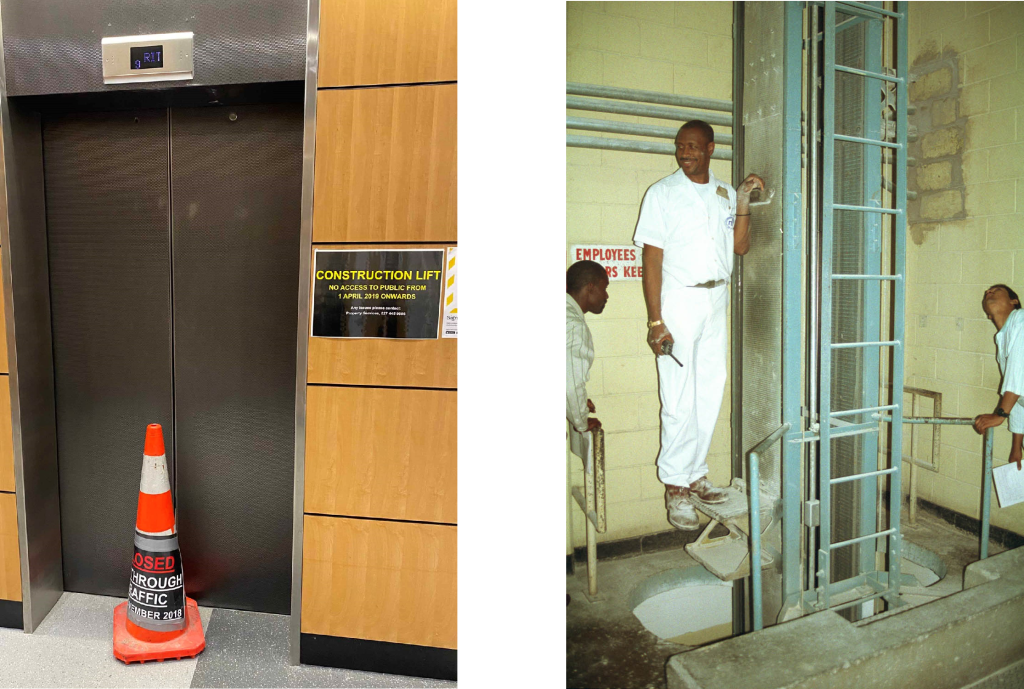
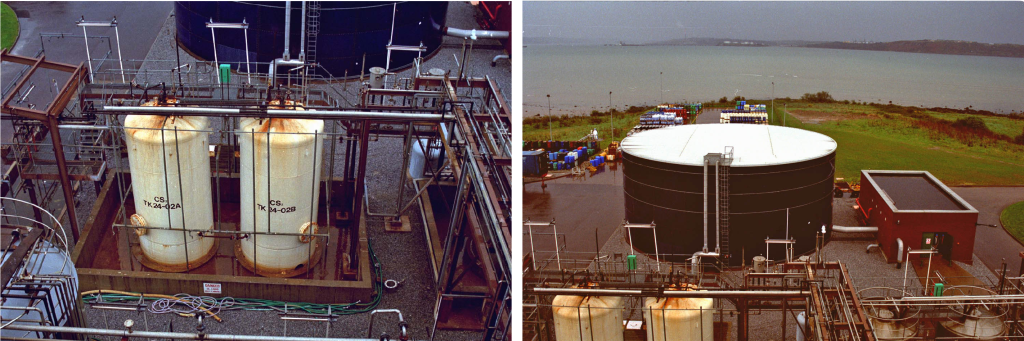
17.3.3 Substances used at work and OHS controls
Read the definition of “substance” in the Health and Safety at Work Act 2015. Hazardous substance has the same meaning as in section 2(1) of the Hazardous Substances and New Organisation Act 1996.
The definition of a substance is very wide and may include things not ordinarily thought of as substances.
Table 29. How to comply with the legislation – hazardous substances
Requirement in the Act and Regulations | What this may require | Examples for safe use of substances |
Eliminating the risk | Stop use of the substance and remove any stored quantities from the workplace | Cease making the product
Change how reactions proceed (speed, temperature, etc) Redesign the process or product and make in-house Contract out the process to a PCBU better equipped to handle the substance |
Substituting (wholly or partly) the hazard giving rise to the risk with something that gives rise to a lesser risk | Use a safer form of the substance | Change the state of the substance from: • gas or vapour to liquid • liquid to solid • dust or nanoparticles to larger particlesChange the temperature of the substance or processRedesign the process or product |
Isolating the hazard from any person exposed to it | Use or store the substance in such a way that workers cannot be affected by it in any hazardous form | Complete enclosure of a process “from bulk tank to finished product” (plus other controls for maintenance) |
Preventing any person from coming into contact with the hazard | Provide a control room isolated from hazards arising from the substance | Place the control room remote from hazards such as explosions, fire, or loss of control events
Have pressurised access to the control room |
Implementing engineering controls | Design the process so the hazard is “locked in” preventing it from escaping and harming workers | Use gas or vapour detection and shutdown systems
Use local extract ventilation systems |
Implementing administrative controls | Safe system of work | Restrict use of a substance to competent workers who have permission to use it
Operate a permit-to-work system for maintenance access Reduce the amount of substance used or stored on site Provide information, training, instruction, supervision (see Table 31) |
Ensuring the provision and use of suitable personal protective equipment (PPE) | As a last resort and based on an effective risk assessment, select, and ensure use of correct PPE | In relation to substances PPE may include: • eye protection • full face protection • hand protection • full forearm protection |
17.3.4 Systems of work and OHS controls
Section 36 HSWA places a duty on PCBUs to provide and maintain a safe work environment and to provide safe systems of work.
The phrase “safe system of work” is not defined in the Health and Safety at Work Act but might be seen by the courts as a plan for how a job gets done safely, based on an assessment of the work to be done and where uncertainty might cause harm to the health or safety of workers.
A safe system of work sets out the precautions needed to eliminate or minimise those risks, including how the work can be done without people being harmed (Braun et al., 2021; Caponecchia & Wyatt, 2021). Sometimes elimination or reduction of risks can lead to the redesign of a job or project in a way that is more efficient.
Table 30. How to comply with the legislation – system of work – this is created from scratch in PB
Requirement in the Act and Regulations | What this may require | Examples for safe use of substances |
Eliminating the risk | Stop the activity using the unsafe system of work | Cease making the product
Redesign the process or product and make in-house Contract out the process to a PCBU better equipped to carry out the work |
Substituting (wholly or partly) the hazard giving rise to the risk with something that gives rise to a lesser risk | Use a safer system of work | Change how work is done (mechanise or automate, reduce manual handling loads)
Include safety by design in the construction sector Redesign the process or product and add some other control if the work still carries unacceptable risk Use water-based paint |
Isolating the hazard from any person exposed to it | Restrict access | Segregate workers and mobile plant using a traffic management plan (WorkSafe NZ, 2021)
Segregate workers at floor level and goods stored at a high level |
Preventing any person from coming into contact with the hazard | Restrict access | Segregate workers and mobile plant
Segregate workers at floor level and goods stored at a high level |
Implementing engineering controls | Change in housekeeping activities | Use industrial floor cleaning equipment
Use handling aids such as hoists and “sack trucks” |
Implementing administrative controls | Safe system of work | Restrict work to competent workers
Operate a permit-to-work system for maintenance access Reduce the amount of substance used or stored on site Provide information, training, instruction, supervision (see Table 31) |
Ensuring the provision and use of suitable personal protective equipment (PPE) |
As a last resort and based on an effective risk assessment, select, and ensure use of correct PPE |
In relation to systems of work, PPE may include: • eye protection • full face protection • hand protection • full forearm protection |
See the WorkSafe guidance on temporary traffic management (WorkSafe NZ, 2021) and a District Court case on such systems (WorkSafe New Zealand v Westown Agriculture Ltd (and Westown Haulage Ltd), 2022). A commercial system that detects reflective strips on hi-vis clothing may provide an additional layer of control of mobile plant or vehicles in workplaces where there may be pedestrians.
17.3.5 Standard operating procedures and safe systems of work as controls
Business-as-usual or one-off activities?
Many business-as-usual jobs can be carried out using a documented standard operating procedure (SOP). Such documentation may also be needed for quality assurance or other purposes, including “safe systems of work” (Braun et al., 2021; Caponecchia & Wyatt, 2021) under the Health and Safety at Work Act 2015.
Example of a standard operating procedure
The photograph shows a standard operating procedure or safe system of work in practice. The workers are handing scaffold poles up from the truck at street level. Two poles are being handed up. Notice that:
- there are always two pairs of hands holding each pole as it progresses up so ensuring each pole is secure
- “clip-on” ladders provide access between levels
- the top level is work in progress and is incomplete
- because a worker could over-balance and fall, each is attached to the scaffolding by a safety line and harness.
Has uncertainty been minimised so far as is reasonably practicable? Is there anything else that could be done that would be
- practicable?
- reasonable?
Such a robust system might be used in other activities where there is no risk of harming people but where a mistake could result in, for example, a major financial loss.
Permit-to-work systems
Procedures for high risk, one-off jobs or project activities may need to be controlled under a robust permit-to-work (PTW) system (FM Global, 2016). Failure of a PTW can result in fatalities, serious injuries (Burlet-Vienney et al., 2015; CSB, 2001b) and major property damage such as the Piper Alpha disaster (Cullen J, 1990). Note: the Cullen report is very large, and you should not attempt to read it unless it is of major interest to you.
While there are similarities between an SOP and PTW, it may not be possible to observe one-off activities or rely on previous experience with such jobs. Therefore, a PTW must be developed following a full risk assessment of the proposed activity.
Permit-to-work is a generic term that includes cold work, entry into confined spaces, hot work, work on electrical systems, work on plant and machinery, work over water, and work with hazardous substances. Each of which may have a separate documented system.
17.3.6 Information, training, instruction, and supervision as administrative controls
These words are not defined in section 36(3)(f) of the Health and Safety at Work Act but Regulation 9 of the Health and Safety at Work (General Risk and Workplace) Regulations (2016) makes detailed requirements; please read these. Also think how “informed consent” (Faden et al., 1986, pp. 274-275) by, for example, participants in adventure activities (ISO21103, 2014), might be covered by section 36(3)(f). Examples are given in the following table.
Table 31. Information, training, instruction, and supervision
Requirement in the Regulations | What this may require | Examples |
Information | Facts or knowledge needed to carry out a task; may be text-based or graphical | Provide instruction manuals
Use checklists: |
Training | Teach a person a particular skill or type of behaviour through regular practice and instruction | Have a training course provided by a supplier, third-party or appointed in-house trainer
Celebrate achievement of a training award (eg, NZQA or similar qualification) Emergency response actions (eg, emergency shutdown) |
Instruction | Give direction or ordering a person to carry out a task in a prescribed manner | Ensure a skilled person provides close direction and supervision of a worker who lacks the necessary competence |
Supervision | Observe and direct the work of a worker; the level and nature of supervision may change as a worker gains competence | Observe the performance of a worker and provide direction or correction to improve performance
As competence increases close supervision diminishes and becomes an occasional check on performance Eventually, the worker achieves required competence and can supervise others |
The use of virtual reality is becoming more widespread in, for example, construction safety training (Rokooei et al., 2023) and NZ electricity lines businesses.
17.3.7 First aid and emergency plans as administrative controls
See also section 7.4 on first aid and emergency planning as part of an occupational health and safety management system.
First aid
First aid provision and emergency plans should be developed as part of a risk assessment for a workplace. Two apparently similar activities may require quite different plans and first aid if one is in a city centre and the other is in a remote rural area.
Read regulation 13 of the Health and Safety at Work (General Risk and Workplace) Regulations (2016) which requires the provision of first aid equipment and facilities. It may also be necessary to train workers in administering first aid. Effective first aid has been shown to reduce the number of injuries in workplaces (Evans, G., 2005; McKenna & Hale, 1981, 1982), perhaps because “first aid training enhances participants’ motivation to avoid occupational injuries and illnesses and improves their risk control behaviour” (Lingard, 2002).
Emergency plans in workplaces
Read regulation 14 of the Health and Safety at Work (General Risk and Workplace) Regulations (2016) which requires the preparation, maintenance and implementation of emergency plans. Integration of such plans with, for example, the requirement for a fire evacuation plan (FENZ, 2018b) or other emergency plans (eg, under clause 8 management system standards (ISO/IEC Annex SL, 2020)), may create efficiencies (Borak & Silverstein, 1999).
17.3.8 Personal protective equipment
Hi-vis clothing as a control
This sub-section was the basis of an article for Safeguard magazine.
Colour or reflective trim?
Combinations of fluorescent colours paired with reflective trim were tested by Sayer & Mefford (2000) under cluttered and uncluttered static conditions while working on a highway during day/night conditions. Their results suggested that a combination of fluorescent yellow and fluorescent orange fabrics gave best colour contrast for the daytime, while silver/white reflective trim gave high luminance for night-time, making the test vests more noticeable.
Later work by Sayer & Mefford (2004) used vehicles being driven on a closed track driven at night through simulated work zones. They found that the configuration and colour of the reflective trim, placement of the garments in the work zone, and driver age significantly affected how conspicuous pedestrians were, but the amount of retroreflective trim had no variable effect. Their report noted, therefore, that “personal safety garments incorporating retroreflective trim significantly improve pedestrian conspicuity in work zones”.
Simple or complex scene?
The importance of “scene complexity” was emphasised in research by Sayer & Buonarosa (2008). In this test, drivers had no idea where the “pedestrians” were but they “were detected at longer distances when the scene was of a lower complexity”. In other words, the more complex the work scene the less effective hi-vis garments were found to be, giving drivers less response time.
Emergency services
First responders may have to work on a highway at night with little or no opportunity to set up a safe environment other than how their vehicles are parked and the hi-vis clothing they wear. In a research project in the USA (Tuttle et al., 2009) vehicles were driven on a closed track during the day and at night. Drivers indicated when they could first see pedestrians who were wearing a safety garment designed to meet NFPA or ANSI/ISEA standards and who were standing or walking in a simulated emergency response scene. In the daytime the pedestrians were seen from greater distances, especially if facing the traffic. There remained no difference in detection distance if the pedestrians were walking or standing still, and both daytime and night-time detection distances remained consistent.
Fatalities in workplaces
How important is poor visibility as a factor in fatalities? Hinze & Teizer (2011) analysed 659 fatalities from a data pool of 13,511 OSHA-investigated cases and identified blind spots (56%), obstructions (23%) and lighting conditions (either too dark (6%) or too bright (1%)) as contributory factors to poor visibility. They also found that nearly 88% of construction fatalities were due to being struck by a moving vehicle, most often a dump-truck, and very often the vehicle was travelling in reverse. Rear view cameras, reversing alarms and proximity alarms were suggested controls.
Maintenance of hi-vis clothing
Regulation 17 of the General Regulations (2016) requires personal protective equipment to be “maintained, repaired, or replaced so that it continues to minimise risk to the worker who uses it”. Some Australian research (Vijayan et al., 2016) tested hi-vis garments after washing and exposure to UV. All the test garments complied with relevant standards after 20 washes but one failed to comply after exposure to UV. This research also found variations in the required hi-vis colours specified for railway workers and contractors. In New Zealand we can experience high levels of UV year-round compared with countries where hi-vis garments may be manufactured. How do hi-vis garments stand up to our high UV levels? Will the initial quality diminish, resulting in hi-vis clothing becoming non-compliant with the specification set by a PCBU?
So what?
These findings may seem obvious now, but before research was carried out, we relied on the claims of manufacturers and “professional judgement” of individual practitioners. We now have some evidence for what it is both practicable and reasonable to implement.
Hi-vis clothing is a form of personal protective equipment. It’s the last item in the hierarchy of control, what we do when all else fails to “minimise the remaining risk”. Perhaps we need to step back and use the research to inspire some lateral thinking about elimination or minimisation before we consider hi-vis clothing.
Visiting a planned site at night can show quite different conditions. What if we carried out effective assessments on workplaces for day and night conditions to identify how to improve the response time for drivers or other workers approaching a workplace? What if an assessment for a temporary workplace – eg, a construction site – identified blind spots and obstructions? Could they be removed? How could we declutter or simplify a workplace? Can we provide pedestrian walkways – even ban pedestrians from workplaces where vehicles operate?
An article in the IOSH Magazine (Warburton, 2017) showed it is both practicable and reasonable to separate workers from vehicles and mobile plant on construction sites. Some PCBUs are already doing just that but research is needed to investigate how such separation would work in New Zealand.
But why bother, why not just stick to using hi-vis clothing? It’s a cheap and easy solution. In an Australian prosecution (DPP v Toll Transport Pty Ltd, 2016) Justice Cannon noted that a worker, Mr Attard, was wearing a hi-vis vest and had ear plugs in his ears when he was killed by a vehicle in a cluttered and noisy workplace where he could not be seen and couldn’t hear the vehicle coming. After his death his employer spent the reasonable amount of A$349,000 on practicable solutions that did not include personal protective equipment. Toll Transport was fined A$1 million.
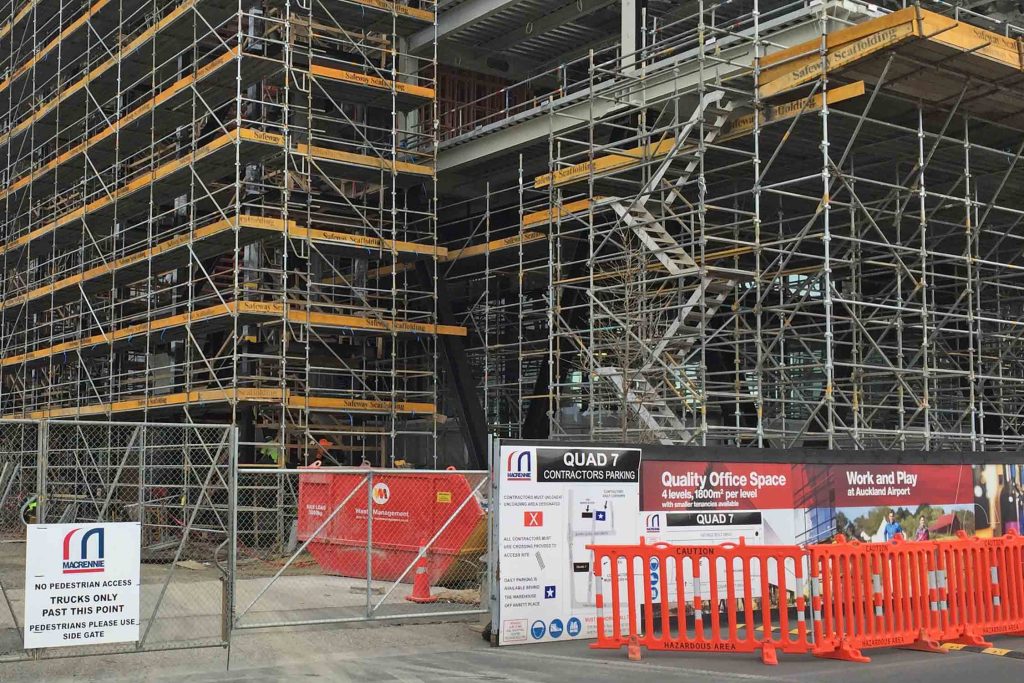
17.4 Inspections as part of administrative controls
See sections 6.2.4 and 21.3.18.
Sudden or catastrophic failure of plant or structures can cause death or serious harm:
- a crew member was killed when a corroded nitrogen gas cylinder failed in service (Maritime NZ v Princess Cruise Lines Ltd, 2019)
- failure to reinstate an interlock and the absence of a regular inspection system resulted in a severe injury to the hand of a worker (WorkSafe NZ v Nicks Components and Accessories, 2018)
- absence of training and an inspection system resulted in amputation of the leg of a worker (WorkSafe NZ v Adams Machinery Plant Hire Ltd and Gordon Developments Ltd, 2016).
Such gradual deterioration of plant such as tanks may be difficult to detect during day-to-day inspections (popularly called creeping crises, boiled frog syndrome, or diffuse disasters), and may result in loss of control of the content of tanks. Between 1996 and 2008 about 5.5% of loss of control events in the UK were estimated to be due to aging plant; some in Europe had the potential to cause major accident events (Horrocks et al., 2010).
In the UK, USA and elsewhere insurance companies provide plant and building inspection services as part of insuring assets. FM Global (2012) provides guidance on recognizing and correcting conditions which could lead to collapse or similar failure of structures or various types of tanks and silos including ‘‘process’’ tanks and silos (eg, holding and storage tanks; fire water tanks; tanks containing flammable liquids or gases; underground tanks, portable tanks. Risk-based inspections have been used increasingly as part of statutory requirements for plant and machinery and especially for pressure vessels (Jackson, 2014).
Management walk-arounds
Safety walk-arounds are one form of inspection. They need to well-structured (Mikkelsen et al., 2010) and go beyond management tours looking for “slips, trips and falls” (Hopkins, 2011).
17.5 Chapter summary
This chapter has covered analysis of uncertainty and its effects on objectives, requirements for and assessment of controls, and three hierarchies of control. In the next chapter we cover evaluation of uncertainty and its effects and relevant treatment if the consequences are assessed as being too great.
17.6 References used in this chapter
Borak, J., & Silverstein, B. D. (1999). Emergency response plans: The benefits of integration. Occupational Hazards, 61(9), 44-48.
Braun, C., Brophy, S., Jassim, M., et al. (2021). A structured approach to the concept of a safe system of work. New Zealand Journal of Employment Relations, 46(2), 4-19. https://doi.org/10.24135/nzjer.v46i2.64
Burlet-Vienney, D., Chinniah, Y., Bahloul, A., et al. (2015, 11//). Occupational safety during interventions in confined spaces. Safety Science, 79, 19-28. https://doi.org/10.1016/j.ssci.2015.05.003
Caponecchia, C., & Wyatt, A. (2021). Defining a “safe system of work”. Safety and Health at Work, 12(4), 421-423. https://doi.org/10.1016/j.shaw.2021.07.001
CSB. (2001b). Refinery Incident – Motiva Enterprises LLC [Incident Investigation report 2001-05-I-DE]. Chemical Safety and Hazard Investigation Board, Washington, DC. http://www.csb.gov/
Cullen J. (1990). The Public Enquiry into the Piper Alpha Disaster (Vol. 2). HMSO. https://www.hse.gov.uk/offshore/piper-alpha-disaster-public-inquiry.htm
DPP v Toll Transport Pty Ltd [2016] VCC1975 Melbourne County Court of Victoria. http://www.austlii.edu.au/au/cases/vic/VCC/2016/1975.html
Evans, G. (2005). HSE survey of first aid training organisations [Research Report RR0358]. Health and Safety Executive, Buxton. https://www.hse.gov.uk/research/publish.htm
Faden, R., Beauchamp, T., & King, N. (1986). A history and theory of informed consent. Oxford University Press.
FENZ (2018b), Fire Safety, Evacuation Procedures, and Evacuation Schemes Regulations. Wellington. http://www.legislation.govt.nz/
FM Global. (2012). Process Tanks and Silos [Property Loss Prevention Data Sheet 1-25]. Author, Johnston, RI. http://www.fmglobal.com
FM Global. (2016). Hot work management [Property Loss Prevention Data Sheet 10-3]. Author, Johnston, RI. http://www.fmglobal.com
Hinze, J. W., & Teizer, J. (2011). Visibility-related fatalities related to construction equipment. Safety Science, 49(5), 709-718. https://doi.org/10.1016/j.ssci.2011.01.007
Hopkins, A. (2011). Management Walk-Arounds: Lessons from the Gulf of Mexico Oil Well Blowout [Working Paper wp79]. Australian National University, Canberra. www.http://ohs.anu.edu.au/
Horrocks, P., Mansfield, D., Thomson, J., et al. (2010). Plant Ageing Study [Research Report RR0823]. Health and Safety Executive, Buxton. https://www.hse.gov.uk/research/publish.htm
HSE. (2014). The health and safety toolbox: How to control risks at work [Guidance Note HSG268]. HSE Books,, Sudbury. http://books.hse.gov.uk/
HSWGR (2016), Health and Safety at Work (General Risk and Workplace Management) Regulations. New Zealand. http://www.legislation.govt.nz/
ISO21103: 2014 Adventure Tourism – Information to Participants, International Standards Organization, Geneva.
ISO31000: 2018 Risk management – Guidelines, International Standards Organization, Geneva.
ISO31073: 2022 Risk management — Vocabulary, International Standards Organization, Geneva.
ISO/IEC Annex SL. (2020). Proposals for management system standards. In Directives, Part 1: Consolidated ISO Supplement – Procedures specific to ISO (11th ed.). International Standards Organization. https://www.iso.org/directives-and-policies.html
Jackson, P. (2014, January). Risky business. Safety & Health Practitioner, 44-46.
Lingard, H. (2002). The effect of first aid training on Australian construction workers’ occupational health and safety motivation and risk control behavior. Journal of Safety Research, 33(2), 209-230. https://doi.org/10.1016/S0022-4375(02)00013-0
Maritime NZ v Princess Cruise Lines Ltd [2019] NZDC 523 Dunedin District Court. https://www.districtcourts.govt.nz/
McKenna, S. P., & Hale, A. (1981). The effect of emergency first aid training on the incidence of accidents in factories. Journal of Occupational Accidents, 3(2), 101-114. https://doi.org/10.1016/0376-6349(81)90003-1
McKenna, S. P., & Hale, A. (1982, 6//). Changing behaviour towards danger: The effect of first aid training. Journal of Occupational Accidents, 4(1), 47-59. https://doi.org/10.1016/0376-6349(82)90055-4
Mikkelsen, K. L., Spangenberg, S., & Kines, P. (2010). Safety walkarounds predict injury risk and reduce injury rates in the construction industry. American Journal of Industrial Medicine, 53(6), 601-607. https://doi.org/10.1002/ajim.20803
Munkman, J. (1975). Employer’s liability at common law (8th ed.). Butterworths.
Rokooei, S., Shojaei, A., Alvanchi, A., et al. (2023, 2023/01/01/). Virtual reality application for construction safety training. Safety Science, 157, 105925. https://doi.org/10.1016/j.ssci.2022.105925
Sayer, J. R., & Buonarosa, M. L. (2008, //). The roles of garment design and scene complexity in the daytime conspicuity of high-visibility safety apparel. Journal of Safety Research, 39(3), 281-286. https://doi.org/10.1016/j.jsr.2007.12.004
Sayer, J. R., & Mefford, M. L. (2000). The effect of color contrast on daytime and nighttime conspicuity of roadworker vests [Research Report UMTRI-2000-35]. Transportation Research Institute, http://deepblue.lib.umich.edu/bitstream/handle/2027.42/49418/umtri-2000-35.pdf?sequence=1
Sayer, J. R., & Mefford, M. L. (2004, //). High visibility safety apparel and nighttime conspicuity of pedestrians in work zones. Journal of Safety Research, 35(5), 537-546. https://doi.org/10.1016/j.jsr.2004.08.007
Tuttle, S. J., Sayer, J. R., & Buonarosa, M. L. (2009, //). The conspicuity of first-responder safety garments. Journal of Safety Research, 40(3), 191-196. https://doi.org/10.1016/j.jsr.2009.03.002
Vijayan, A., Islam, S., Jones, M., et al. (2016). Degradation of fluorescent high-visibility colors used in safety garments for the Australian railway industry. Journal of Safety Research, 56, 1-7. https://doi.org/10.1016/j.jsr.2015.11.008
Warburton, N. (2017, October). Three degrees of separation. IOSH Magazine, 36-40.
WorkSafe NZ. (2021). Managing work site traffic [Guidance Note 4]. Author, Wellington. https://www.worksafe.govt.nz/
WorkSafe NZ v Adams Machinery Plant Hire Ltd and Gordon Developments Ltd [2016] Auckland District Court. https://www.districtcourts.govt.nz/
WorkSafe NZ v Nicks Components and Accessories [2018] North Shore District Court. https://www.worksafe.govt.nz/laws-and-regulations/prosecutions/court-summaries/nicks-components-and-accessories-limited/
WorkSafe NZ v Westown Agriculture Ltd (and Westown Haulage Ltd) [2022] NZDC 22256 District Court, New Plymouth. https://www.worksafe.govt.nz/laws-and-regulations/prosecutions/court-summaries/westown-haulage-and-westown-agriculture-limited/