15 Risk assessment process: Identification
15.1 Chapter overview
Cross reference to ISO31000 clause 6.3 and ISO45001 clauses 6.1 and 8.1.
Check for key readings, webinars, and videos for complementary resources.
Definitions of italicised terms are in the Glossary.
Relevant law
- Health and Safety at Work Act 2015
- Health and Safety at Work (General Risk and Workplace Management) Regulations 2016
Key questions
What is or will be the impact of artificial intelligence on the business?
If risk is the “effect of uncertainty on objectives”:
- What are the objectives of the organisation, activity, system, or item?
- What uncertainties could affect achievement of those objectives?
Useful management techniques
NB: the following is a small selection of techniques that may be useful.
- 5W1H (see section 21.3.1)
- Bowtie analysis (see section 21.3.3)
- Brainstorming (see section 21.3.4)
- Fault tree analysis (see section 21.3.11)
- Flowcharting or process mapping (see section 21.3.13)
- HAZOP analysis (see section 21.3.15)
- Inspections, physical surveys, and observations (see section 21.3.18)
- Risk breakdown structure (see section 21.3.33)
- Structured what-if-then, abbreviated to SWIFT (see section 21.3.38)
15.2 What is risk identification?
Two important notes
Sometimes,
- “effects of uncertainty on objectives” (risks) will be found by researching and writing a well-developed context statement (Chapter 14)
- risk identification blurs into risk analysis (Chapter 17).
Often a health and safety practitioner will lack the competence to do more than identify causal factors of harm: see WorkSafe NZ v Precision Animal Supplements Ltd (2018b) where the judge commented about the consultant.
The company underwent onsite audits in … February 2017. The dates over which the offending occurred fall within that last period. There were recommendations from the audits emanating from the consultants. The health and safety consultant engaged did not have the experience in health risk management or hazardous substances risk management.
A generalist health and safety practitioner may have the competence to identify causal factors but not to analyse and advise on the potential for harm. Failure to identify causal factors and their effects on occupational health and safety objectives will mean that no action can be taken to manage such risks.
Risk identification defined
Risk identification is the “process of finding, recognising and describing risks” (ISO31000, 2018). Substituting in the definition of risk gives: “process of finding, recognising and describing effects of uncertainty on objectives”.
While we are especially interested in OHS objectives, remember that the standard also says that “objectives can have different aspects such as financial, health and safety, and environmental goals and can apply at different levels such as strategic, organisation-wide, project, product, and process”. Therefore, we should look widely for uncertainties about achieving those objectives and how there might be knock-on effects on OHS.
Legal requirements
The Health and Safety at Work (General Risk and Workplace) Regulations (2016) require in Regulation 5 “Duty to identify hazards: A PCBU, in managing risks to health and safety, must identify hazards that could give rise to reasonably foreseeable risks to health and safety”. We can think of a hazard as being the potential cause of an event. If we also include the source of such a causal factor, we get a rich understanding of how an event can be caused.
15.2.1 Suggested identification process and techniques
A suggested risk identification process and techniques are set out in the process map Figure 40, and may include running a workshop with knowledgeable people. You may be able to develop a mind map for topics of special interest to you or your organisation. This is an alternative to a checklist and has the advantages that users:
- cannot just “tick boxes”, but
- can see the bigger picture, and
- may suggest additions.
Try to think of causal factors that may be some distance away physically, or in the supply chain, that might have a local impact.
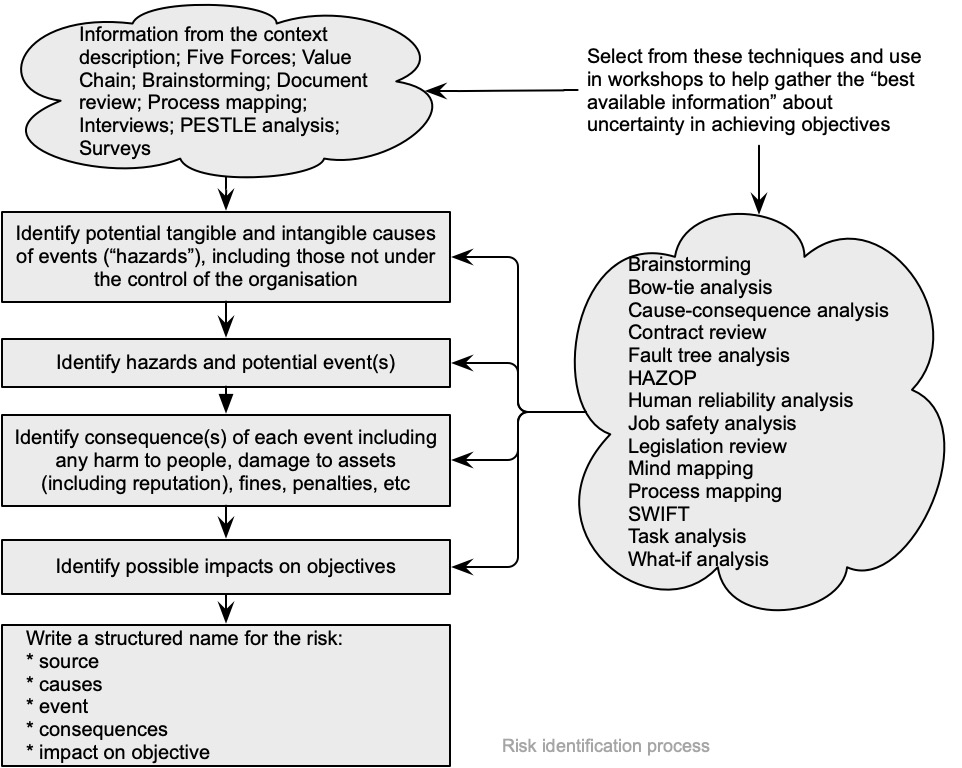
An event (ISO31073, 2022) is an “occurrence or change of a particular set of circumstances”. It can be one or more occurrences and can have several causes; or an event might consist of something not happening. After an event has occurred it might be called an “incident” or “accident”; and an event without consequences can also be referred to as a “near miss”, “incident”, ‘near hit’ or “close call”.
Sometimes consequences may not obviously affect objectives because relevant objectives have not been set. If you cannot link consequences with objectives, you will need to consult with stakeholders and ask why.
15.3 Identification of causal factors of slips, trips, and falls
Slips, trips and falls (STF) account for a large number of injuries in workplaces every year. Falls from a height and STF on the level are significant causes of injury and ACC claims during house construction in New Zealand (Tappin et al., 2004) and internationally (Tanvi Newaz et al., 2022). Some STF result in apprarently minor harm while others are fatal. The WorkSafe NZ website gives relatively little information about causal factors of slips, trips and falls and suggests visiting the UK HSE website.
An academic article (Aneziris et al., 2008) and some HSE research reports (eg, Mason, 2003; Peebles et al., 2005; Scott, 2004, 2005; Tappin et al., 2004) were used to develop Figure 41 to help take a structured approach to the causes of slips, trips and falls. Note that dry contaminants such as flour in the food industry and dusts in the construction industry can also be significant causes of pedestrian slips (Houlihan et al., 2009).
Spearpoint & Hopkin (2020) identified three key causal factors leading to a fatality due to a fall from a height (distance fallen, age of the injured person, and the impact surface) included in Figure 41.
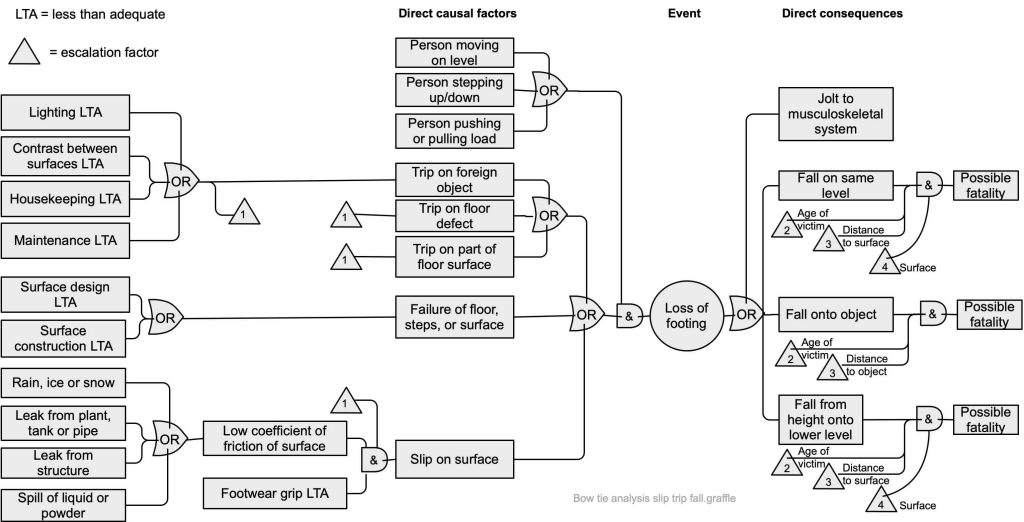
Regular inspections will help identify causal factors (Fox, 2010; Scott et al., 2006) and the number of slips and trips then can be reduced by targeting housekeeping, maintenance (eg, repairing vehicle and machinery oil leaks and filling in potholes) and reviewing procedures during wet weather.
HSE has carried out several research projects investigating testing the slip potential of floors (Darby, 2012; Shaw, 2007a, 2007b; Shaw et al., 2009). Other research has considered the effectiveness of footwear as a form of personal protective equipment that can help minimise slips (Cockayne et al., 2021; Fox, 2010; Frost et al., 2022; Hunwin, 2012; Liddle, 2009), the effectiveness of cleaning regimes (Hallas & Shaw, 2005) and the effects of microclimate conditions on the slip potential for flooring (BSRIA Ltd, 2006).
Other work has been carried out on the slip resistance of floors (Loo-Morrey, 2006, 2007; Loo-Morrey & Lemon, 2007), the effectiveness of information provided by manufacturers of footwear and flooring (Liddle, 2009) and access equipment for construction work (Gervais & McCann, 2013).
Cases of interest
A club was prosecuted when a patron fell from an unfenced loading dock (WorkSafe NZ v Waipa Workingmen’s Club Incorporated, 2016). An Australian common law case (Gollan, 2022) found that an occupier was liable for a slip on stairs that did not comply with the Building Code, and in a similar case (Wolters Kluwer Australia, 2021) a holiday home owner was liable for an injury caused by falling off a veranda.
15.4 Identification of causal factors of occupational ill-health
The following mind map shows some examples of occupational health hazards, adapted from Benke & Cross (2019, pp. 43-44). These are explored in more detail in HLWB508 Human and Biological Factors in Workplace Health and Safety. See Cherrie (2023) for further thoughts on occupational exposure science.
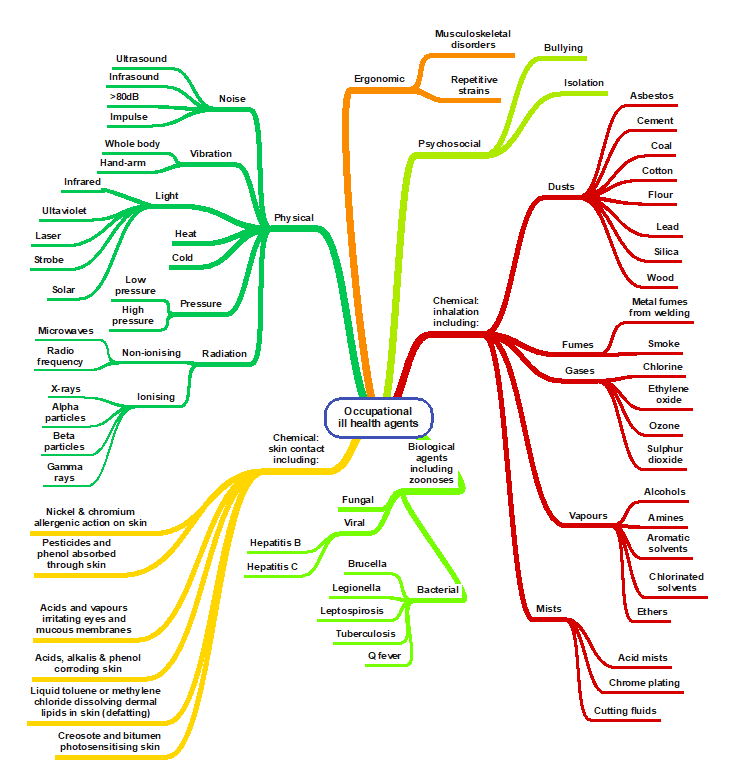
The British HSE has published many research reports of relevance, including manual handling of recyclable waste (Pinder & Okunribido, 2019), emissions from polymer filament desktop 3D printers (Hall et al., 2019), metal working fluid mist (Bailey et al., 2022), worker fatalities in the waste and recycling industry (Beards et al., 2018), and occupational health and extended working lives in the transport sector (Fox et al., 2017). Incapacity from work due to “gradual process, disease, or infection” may become an ACC claim subject to section 30 of the Accident Compensation Act 2001.
Figure 42 will need revision as climate change results in higher temperatures and humidity (Kjellstrom et al., 2018).
15.5 Identification of human and performance shaping factors
Human and performance-shaping factors are important sources of uncertainty. The subject is covered in more detail in paper HLWB508 Human and Biological Factors in Workplace Health and Safety but some key issues for risk identification are covered here.
Performance-shaping factors are the “characteristics of the external environment, of the task and of humans that shape individual performance” and “include general conditions which may influence error probability, but do not cause errors” such as organisational, job and individual worker factors (IEC62508, 2015). Figure 43 below expands on these factors to show more detail because they often are under the direct control of a PCBU. Performance-shaping factors are a common concern in occupational safety and related fields, but they are often overlooked as causal factors in other areas of risk. By changing them, we can improve wellbeing and performance at work.
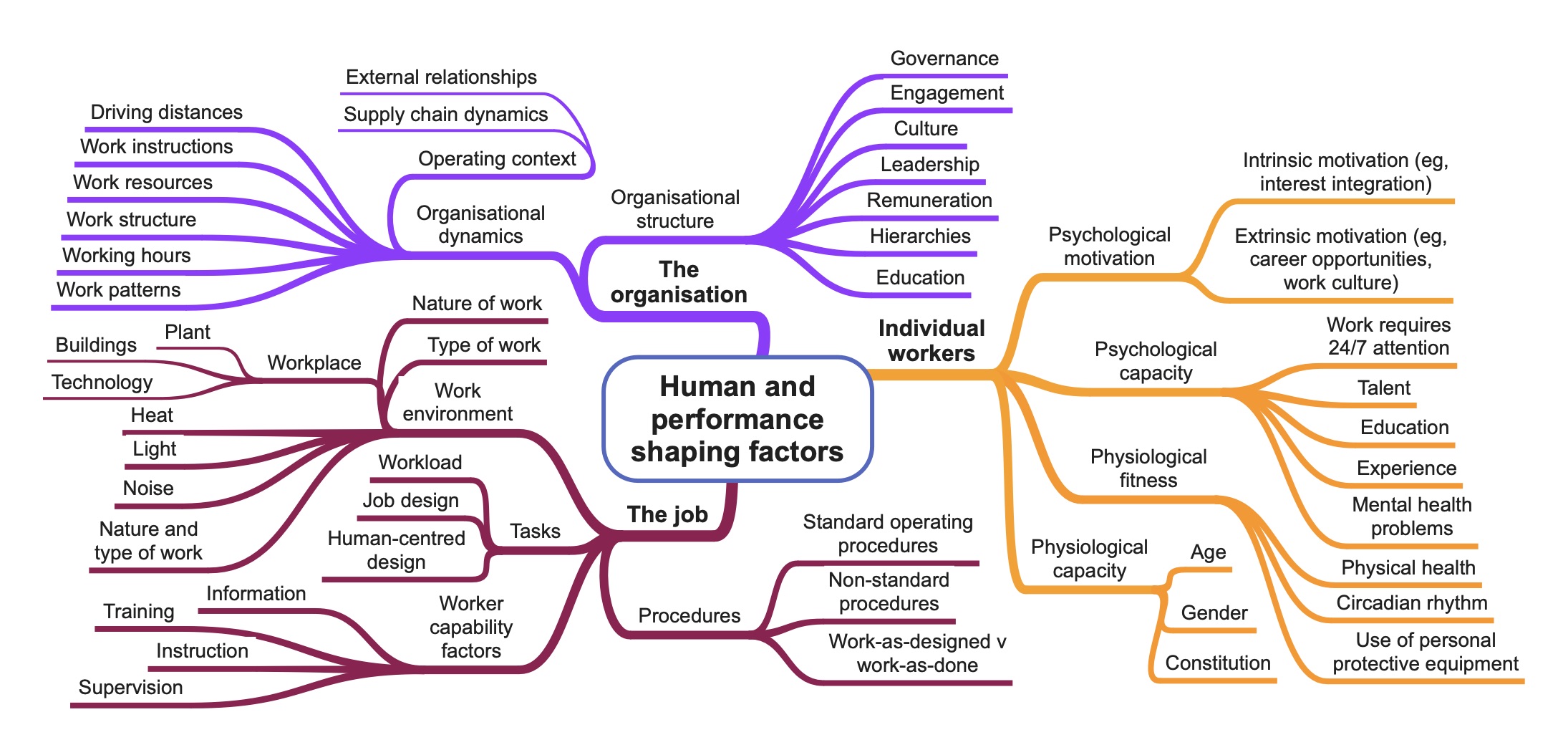
Source: Developed by author using HSE (1999), IEC 62508 (2015) and Safe Work Australia (2022)
15.5.1 Monitoring and review of human and performance-shaping factors
Any new or changed job should be monitored by the team leader or others to ensure the new operating procedure has become a standard operating procedure.
Review human factors or performance shaping factors when:
- incidents involving employees, contractors, or visitors where “human error” is given as a cause
- there are high sickness absence rates
- there are high staff turnover rates
- there is a low level of, or reduction in, compliance with health and safety rules
- behaviour or performance factors are identified in risk assessments
- there are complaints about stress, bullying or other psychosocial issues
- there are high or increasing employee complaints about working conditions or job design.
Court case of interest
A New Zealand court case of interest (Yoon Cheol Hong v Chevron Traffic Services Ltd, 2019) was heard in the Employment Court but also illustrates breaches of sections 45(a) and 45(b) of the Health and Safety at Work Act. Mr Yoon Cheol Hong was employed by Chevron Traffic Services Ltd as a traffic controller. He violated rules about how to get out of a truck and how to control traffic and was summarily dismissed. In the Employment Court his dismissal was found to have been reasonable and costs were awarded to Chevron.
15.5.2 “Human error”
The dependability of any work-related system may be greatly influenced by the human aspects of the system. “Human errors” when operating or interacting with systems have been implicated as causal factors in many incidents and, if “human errors” are taken to include violations, it can be argued they have also caused major financial and other non-safety incidents.
However, Dekker (2014, p. xix) insists we should put “human error” in quote marks as it “is no more than a label … a judgement … an attribution that we make, after the fact, about the behaviour of other people, or about our own”. Dekker also strongly argues that “there is no such thing as ‘pilot error’, ‘operator error’ or any other form of ‘human error‘ as people do not set out to commit an error – there are always contributory causes”. This approach is different from attributing blame to “human error” (something negative and undesirable) and recognises that people and organisations are not perfect. This contrast between the old and new ways of thinking about “human error” is summarised in the following table.
Table 16. The old and new views of human error
Old view | New view |
“Human error” is the cause of trouble | What we call “human error” is a symptom of deeper trouble |
“Human error” is a separate category of behaviour, to be feared and fought | “Human error” is an attribution, a judgement that we make after the fact |
“Human error” is the target; people’s behaviour is the problem we need to control | Behaviour is systematically connected to features of people’s tools, tasks, and operating environment |
“Human error” is something to declare war on. People need to practice perfection | “Human error” is information about how people have learned to cope (successfully or not) with complexities and contradictions of real work |
“Human error” is a simple problem; once all systems are in place just get people to pay attention and comply | A “human error” problem is at least as complex as the organisation that helps create it |
With the right procedures, compliance, technology, and supervision, we can reduce the “human error” problem | With a better understanding of the messy details of people’s daily work we can find ways to make it better for them |
We can achieve zero errors, zero injuries, zero accidents | We can enhance the resilience of our people and organisation |
Reason (1990) helped develop a deeper understanding of “”human error“”. He called error “a generic term to encompass all those occasions in which a planned sequence of mental or physical activities fails to achieve its intended outcome, and when these failures cannot be attributed to the intervention of some chance agency”(Reason, 1990, p. 9), while IEC62508 (2015) defines “Human error” as the “discrepancy between the human action taken or omitted, and the action intended”.
The contributory causes and the reasons for such failures often are not the “fault” of the worker. The root cause may well lie in the organisational structure or dynamics, possibly distant in time or place, from where the so-called “human error” happened. The design of a task and a standard operating procedure, (“work as imagined”) may be such that it cannot be carried through in the work environment and a worker has to interpret the planned work to suit the situation (“work as done”). These environmental issues are performance-shaping factors – the “characteristics of the external environment, of the task and of humans that shape individual performance” (IEC62508, 2015) and “include general conditions which may influence error probability, but do not cause errors” (Rasmussen, 1997). They suggest that human factors and occupational health and safety management systems are parts of wider organisational management issues (Bellamy & Geyer, 2007, pp. 131-132; Munkman, 1975).
The study of such human factors (also called ergonomics) is the “scientific discipline concerned with the understanding of interactions among human and other elements of a system that applies theory, principles, data and methods to design in order to optimise human well-being and overall system performance” (IEC62508, 2015).
15.5.3 Classification of “human errors”
Reason (1990, p. 9; 1998) described slips of actions and memory lapses as “errors which result from some failure in the execution and/or storage stage of an action sequence, regardless of whether or not the plan which guided them was adequate to achieve its objective”. He also described mistakes as “deficiencies or failures in the judgemental and/or inferential processes involved in the selection of an objective or in the specification of the means to achieve it, irrespective of whether or not the actions directed by this decision-scheme run according to plan”. These are broadly summarised in Figure 44. See Zarei et al (2023) for a research-based taxonomy of performance-shaping factors.
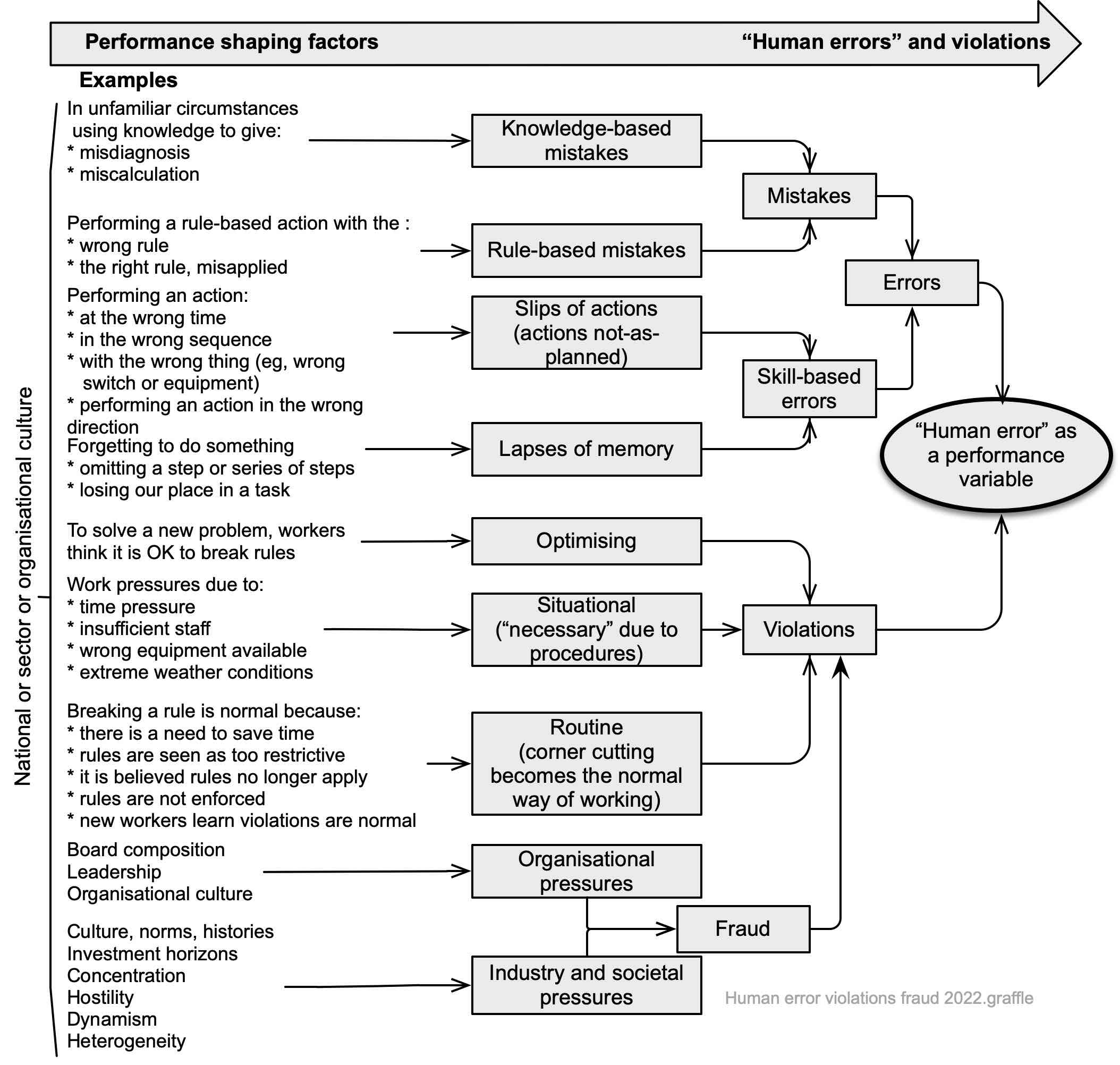
Figure 44 suggests that we progressively convert new knowledge into rules to help us carry out tasks. Those rules become part of our skill-based competencies and are the least error-prone. However, sometimes rules can lead us to repeatedly use a skill in the wrong circumstances or otherwise make errors that are skill-based. Such errors are performance variables or deviations from the expected.
For an example of a probable lapse of memory see Hoey (2017) where “the rail protection officer’s error was highly likely a lapse in memory influenced by the pressures he was under in his role as team leader”. Woodcock (2007) analysed more than 5,000 fairground rides and found a rider error rate of 1.4%, most often as violations of rules to not extend limbs.
In summary, and as a very broad and simplistic generalisation, we make:
- knowledge-based errors on about one occasion in 10 when using new knowledge
- rule-based errors on about one occasion in 100 after changing the knowledge into a rule
- skill-based errors on about one occasion in 1000 when rules have become skills.
If we know (indeed, should expect) the above performance variables we should design systems and tasks that have built-in resilience to errors.
15.5.4 Observed error and violation rates
Error and violation rates for people can sometimes be very high, making adverse consequences almost certain if preventative or detective controls are inadequate. Table 17 sets out some common tasks and indicative error rates for well-managed activities supported by good training and standard operating procedures in a well-controlled work environment. These are a guide only and will almost certainly be different in any organisation not meeting these criteria.
Table 17. Generic tasks and associated error probabilities
Generic Tasks | Assessed error probability | Number per 1,000 instances |
Totally unfamiliar activity performed at speed with no idea of the likely consequence | 0.55 | 550 |
Failure of a supervisor to notice a worker’s error (eg, failure to close a valve) | 0.5 | 500 |
Move or restore a system to a new or original state on a single attempt without supervision or standard operating procedure | 0.26 | 260 |
Complex task requiring a high level of comprehension and skill | 0.16 | 160 |
Fairly simple task performed rapidly or given scant attention | 0.09 | 90 |
Open the wrong valve or too many valves | 0.04 | 40 |
Re-open a valve at the wrong time | 0.03 | 30 |
Failure to respond to a normal alarm | 0.02 | 20 |
Failure to replace a printed circuit board correctly | 0.004 | 4 |
Restore or shift system to original or new state following standard operating procedure, with some checking | 0.003 | 3 |
Leave the light on | 0.003 | 3 |
Read a checklist or digital display wrongly | 0.001 | 1 |
Tanker driver drives away despite delivery being incomplete | 0.0005 | 5 |
Driver fails to notice major crossroad | 0.0002 | 0.2 |
Routine task with care needed: | ||
• Failure to act correctly after one minute in an emergency | 0.9 | 900 |
• Failure of new work shift to check hardware unless specified | 0.1 | 100 |
• Wrongly read a five-letter word with poor resolution | 0.03 | 30 |
• Wrong selection from a vending machine | 0.02 | 20 |
• Do simple algebra wrongly | 0.02 | 20 |
• Do simple arithmetic wrongly | 0.01-0.03 | 10-30 |
• Record information or read a graph wrongly | 0.01 | 10 |
• Let the milk boil over | 0.01 | 10 |
Violations shown in Figure 44 may be routine (“that’s what we all do” because violations are rarely punished), situational (“no time to do this the right way”) or exceptional (“never seen one like this before, I’ll use my initiative”) (Bates & Holroyd, 2012; Reason, 1990, pp. 196-197). The diagram includes causal factors of fraud because fraud is also a violation of rules. Certainly, industry pressures seem quite like routine violations and societal pressures look somewhat like exceptional violations. See the report by Sheedy et al (2017) on profit-based incentives.
Some estimated, generic violation rates are suggested in Table 18 below.
Table 18. Generic violation rates
Generic violation behaviours | Assessed error probability | Number per 1,000 instances |
Distinctly inconvenient to comply, violator does not feel bound to comply, easy to violate, little likelihood of detection | 0.42 | 420 |
Personal benefits of violation are high and direct | 0.38 | 380 |
Compliance relatively unimportant, easy to violate, few/no inducements to comply | 0.35 | 350 |
Personal benefits in violating even though likelihood of detection is moderate to high | 0.18 | 180 |
Personal benefit in violating though likelihood of detection is moderate/high OR compliance is important but chances of detection of violation are low | 0.18 | 180 |
Compliance important, usually legally required, chances of detection are low/moderate | 0.03 | 30 |
No immediate incentive to violate but likelihood of detection moderate/high | 0.007 | 7 |
Socially unacceptable, low likelihood of detection: low likelihood of unfavourable outcome for violator | 0.007 | 7 |
Socially unacceptable, chances of detection high, chances of adverse outcome high | 0.0001 | 0.1 |
A simple worked example
In fault tree A below, a worker may make a “human error” once in every 1,000 activities (1 in 1,000). They are supported by an electronic warning system with an error rate of 1 in 1,000 activities (work as imagined). The combined error rate is 1 in 1,000,000 (ie, 1,000 x 1,000). In fault tree B, the warning system is switched off or has failed (error rate is 1) resulting in an overall error rate of 1 in 1,000 (ie, 1 x 1,000).
Management may assume that the worker and the warning system are both performing as intended but the error rate is considerably higher than expected and, if the worker places reliance on the warning system, their error rate could be worse than 1 in 1000 (work as practiced).
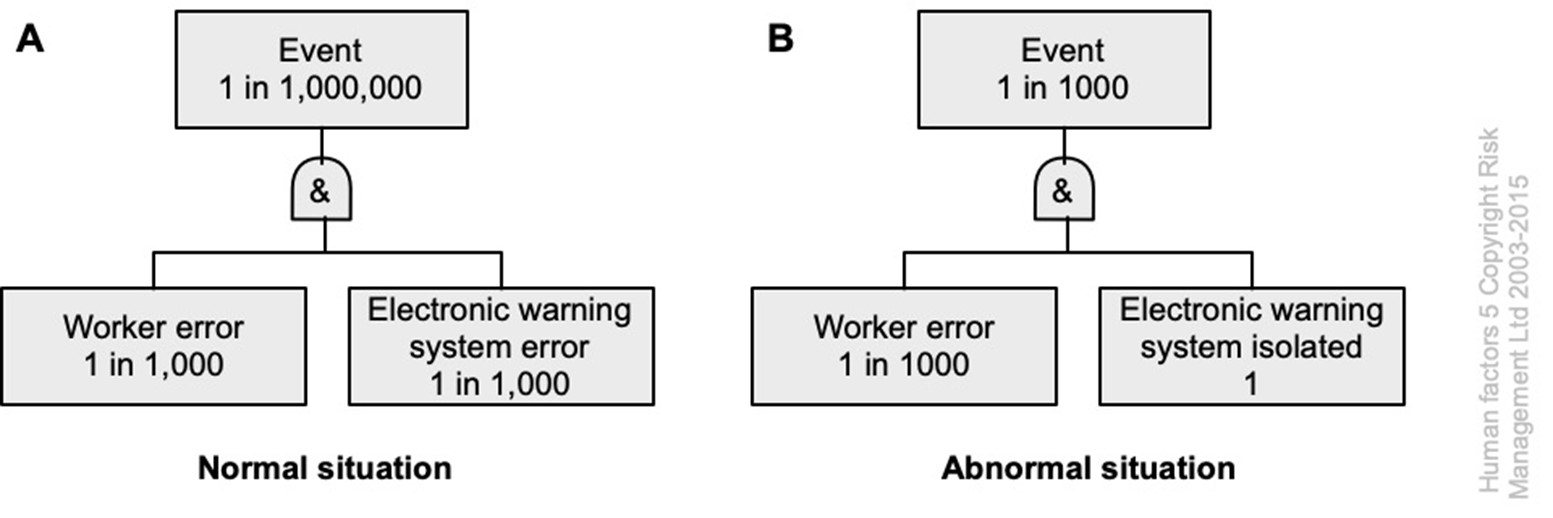
15.5.5 Psychosocial harm
Figure 46 is adapted from ISO45003. Refer to the standard for detailed information about causes and consequences. See (Hodge & Bowler, 2023) for an Australian prosecution following a suicide.
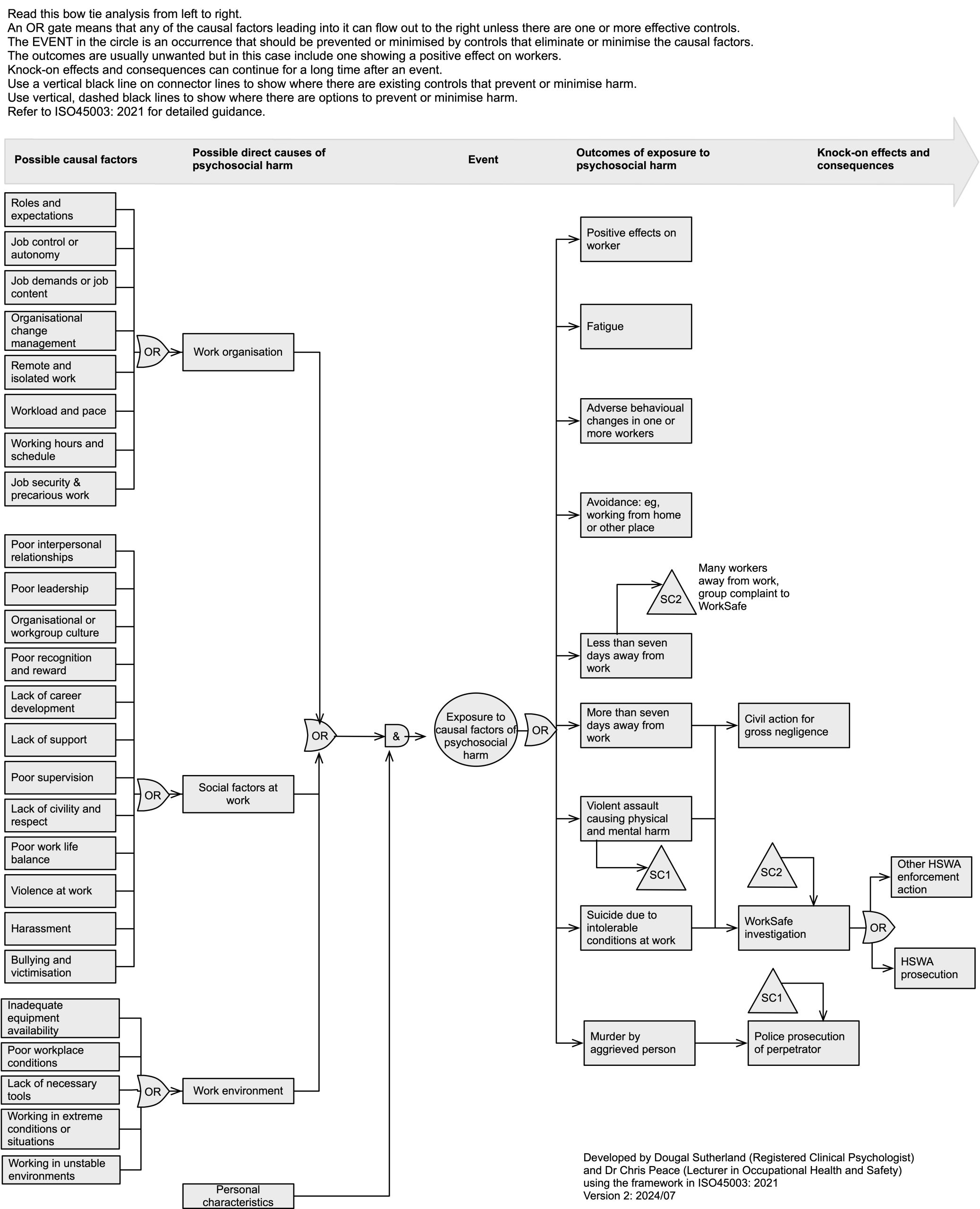
15.5.6 Biases
The following are some of the biases that adversely affect our judgement.
Table 19. Some important biases
Action-oriented biases | Excessive optimism: the tendency for people to be over-optimistic about the outcome of planned actions, to overestimate the likelihood of positive events, and to underestimate the likelihood of negative ones | Overconfidence: overestimating our skill relative to others’, leading us to underestimate our ability to affect future outcomes, take credit for past outcomes, and neglect chance | Competitor neglect problem: the tendency to plan without factoring in competitive responses, as if one is playing tennis against a wall, not a live opponent |
---|---|---|---|
Interest biases | Misaligned individual incentives: incentives for individuals in organisations to adopt views or to seek outcomes favourable to their unit or themselves at the expense of the overall interest of the organisation; these self-serving views are often held genuinely, not cynically | Inappropriate attachments: emotional attachment of individuals to elements of the business (eg, legacy products or brands) creating a misalignment of interests | Misaligned perception of corporate goals: disagreements (often unspoken) about the hierarchy all relative weight of objectives pursued by the organisation and about the trade-offs between them |
Pattern-recognition biases | Confirmation bias: the over-weighting of evidence consistent with a favoured belief, underweighting of evidence against a favoured belief, or failure to search impartially for evidence | Power of storytelling: the tendency to remember and to believe more easily a set of facts when they are presented as part of a coherent story | Management by example: generalising based on examples that are particularly recent or memorable |
Champion bias: the tendency to evaluate a plan or proposal based on the track record of the person presenting it, more than on the facts supporting it | False analogies – misleading experiences: relying on comparisons with situations that are not directly comparable | Cognitive bias: people with little expertise or ability assume they have superior expertise or ability. Failure to seek better or alternative information. The “Dunning-Kruger effect” | |
Stability biases | Anchoring and insufficient adjustment: rooting oneself to an initial value, leading to insufficient adjustments of subsequent estimates | Sunk-cost fallacy: paying attention to historical costs that are not recoverable when considering future courses of action | Loss aversion: the tendency to feel losses more acutely than gains of the same amount, making us more risk-averse than a rational calculation would suggest |
Status quo bias: preference for the status quo in the absence of pressure to change it | Hindsight bias: in retrospect, people believe what happened was inevitable | ||
Social biases | Groupthink: striving for consensus at the cost of a realistic appraisal of alternative courses of action | Sunflower management: tendency for groups to align with the views of their leaders, whether expressed or assumed | Self-serving bias: bad luck is blamed for failures, while successes are attributed to personal skill |
15.5.7 Inattentional blindness
We may suffer from “inattentional blindness” due to:
- our psychological capacity to pay attention (we can hold 7± 2 actions in our working memory at any one time (Miller, G., 1994) – sometimes called “bounded rationality” (Simon, 1979)) – and adding one new action may result in forgetting to carry out an original action
- our mental workload (we find it difficult to carry out two demanding tasks at the same time)
- our expectation that the future will be the same as the past
- lack of conspicuousness (the less contrast there is between an object and its background the less likely we are to see or respond to it).
As a result workers may fail to carry out a task as intended. This can be overcome by better design of an activity, system, subsystem, unit, or part to help improve the situational awareness of workers.
15.5.8 Active and latent failures
Seeing human error as a performance variable helps us understand when the consequences of such variation can be felt. The diagram below shows correctly performed tasks, variations in task performance that are detected, and variations that are not detected.
When variations are detected, we can recover from them, tolerate them, or ignore them. Such variations may be called “active failures” and typically will be found in frontline activities. If such variations are not detected they may persist in a system for long periods of time (years, even decades) as “latent failures”. These may be caused by designers, decision makers or managers.
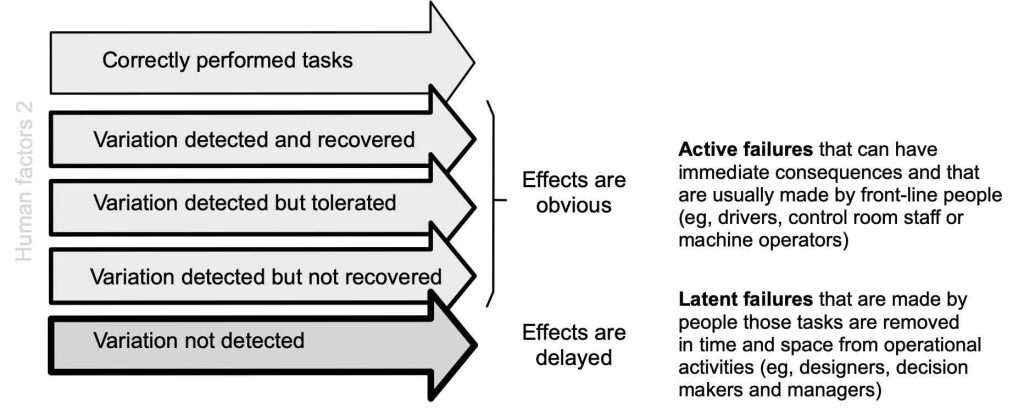
Example
Racking for the storage of steel tube was designed and made in 1969 in one factory. It was made from the wrong steel.
In 1993 it was in use in another factory when it failed due to fatigue (a latent failure) and dropped 5 tonnes of steel on a 65-year-old worker who was about to retire.
15.5.9 Resident pathogens and Normal Accident Theory
Resident pathogen
Major disasters are rarely, if ever, due to a single causal factor and, in complex systems, there are many opportunities for minor variations to converge in a single point of time and place (Turner, 1978). Each of those variations can be thought of as a “resident pathogen” that, in some unforeseen circumstance, contributes to the breakdown of a system (Reason, 1990).
Normal Accident Theory
Perrow (1999, pp. 356-357) developed “Normal Accident Theory” from the convergence of such factors in closely coupled, complex systems.
Nothing is perfect, neither designs, equipment, procedures, operators, supplies, or the environment. Because we know this, we load our complex systems with safety devices in the form of buffers, redundancies, circuit, breakers, alarms, bells, and whistles. Small failures go on continuously in the system, since nothing is perfect, but the safety devices and the cunning of designers and the wit and experience of the operating personnel, cope with them. Occasionally, however, two or more failures, none of them devastating in themselves in isolation, come together in unexpected ways and defeat the safety devices – the definition of a “normal accident” or system accident. If the system is also tightly coupled, these failures can cascade faster than any safety device or operator can cope with them, or they can be incomprehensible to those responsible for doing the coping. If the accident brings down a significant part of the system, and the system has catastrophic potential, we will have a catastrophe. That, in brief, is Normal Accident Theory.
15.6 Identification of causal factors of fire
Figure 48 (source: author) below is a generic fault tree analysis for fire; further information about fault tree analysis is in section 22.3.11. Fire safety in construction (HSE, 2022) and work-related fatalities and injuries due to fire (Kool, 2001) may need to be considered in some PCBUs.
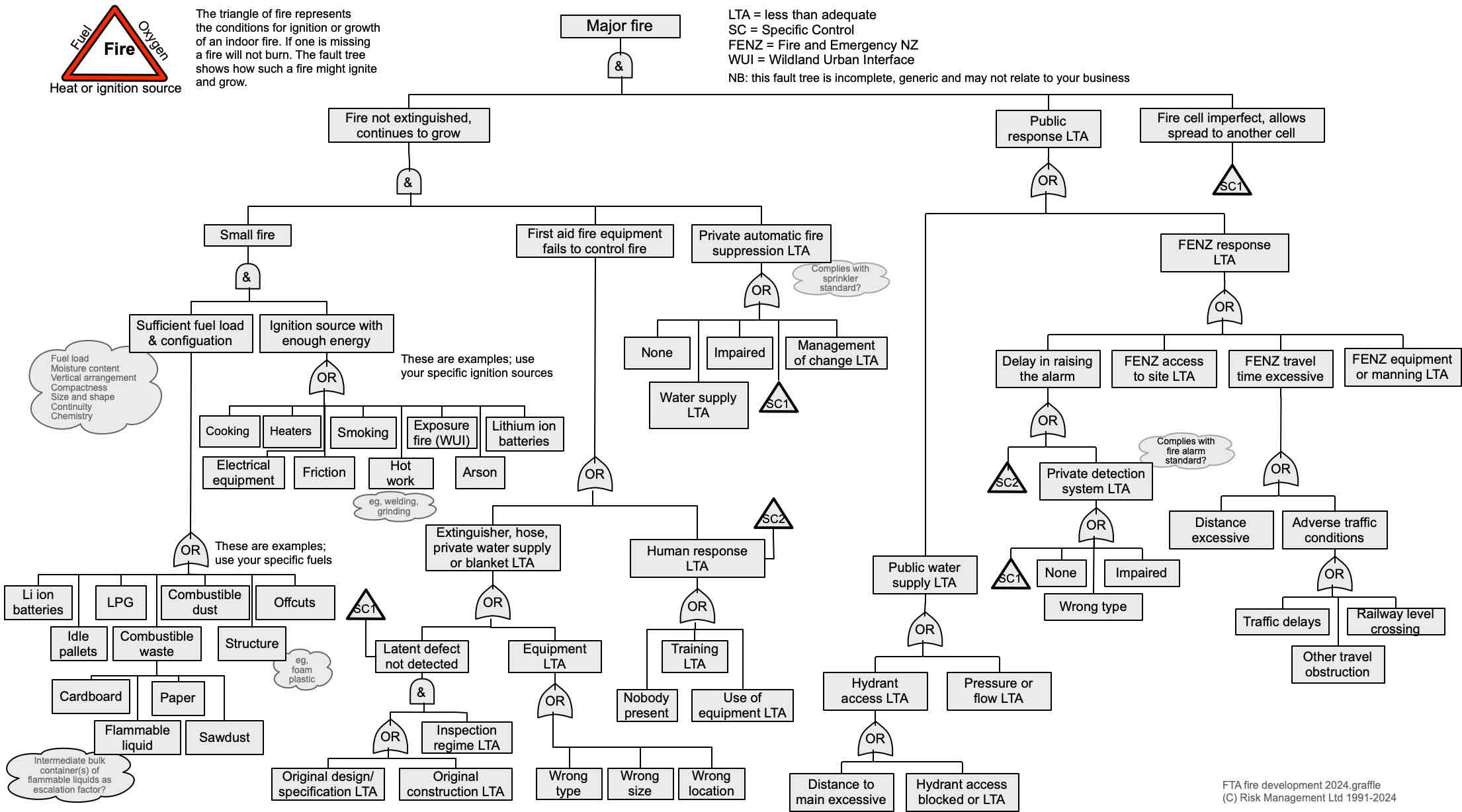
15.7 Identification of causal factors of explosions
This brief subsection outlines the causal factors and consequences of explosions.
15.7.1 Definitions
An explosion is the rapid conversion of physical or chemical energy into mechanical energy resulting in the violent expansion of gases and creation of a blast wave with an overpressure and duration that depend on the type of explosion (FM Global, 2013).
A physical explosion can be due to sudden failure of a pressurised vessel (eg, a boiler) or rapid boiling of water contacting a very hot metal (1 litre of water is approximately 1720 litres of steam).
A chemical explosion is a reaction such as a flammable vapour or fine dust rapidly burning in air.
A thermal explosion is the result of an exothermic reaction in a confined space with inadequate cooling. As the temperature rises the reaction speeds up releasing more heat until the vessel fails.
Failure of a vessel (eg, fire impinging on an LPG tank weakening the tank wall) that is above its atmospheric boiling point can result in a boiling liquid expanding vapour explosion (BLEVE). If the liquid is flammable a fireball may occur.
A deflagration is very rapid heating of material by convection, conduction and radiation resulting in it burning away. However, the speed of burning is less than the speed of sound unless the unburned material is confined. Confinement then can result in detonation.
A detonation is an exothermic reaction that proceeds more quickly than the speed of sound, resulting in a shock wave that maintains the explosion.
An implosion occurs because the internal pressure in a vessel is less than the external pressure and the vessel collapses inwards (FM Global, 2002). For example, steam in a tank condenses to form water but the vent pipe is blocked, preventing entry of air, and the tank crumples.
Mechanism of an explosion
An explosion proceeds through three stages during which (see Figure 49):
- energy or fuel builds up until there is sufficient to produce an overpressure if triggered
- during the build-up stage the triggering agent is absent but, when introduced, triggers the explosion
- the explosion releases sufficient energy to cause damage and harm.
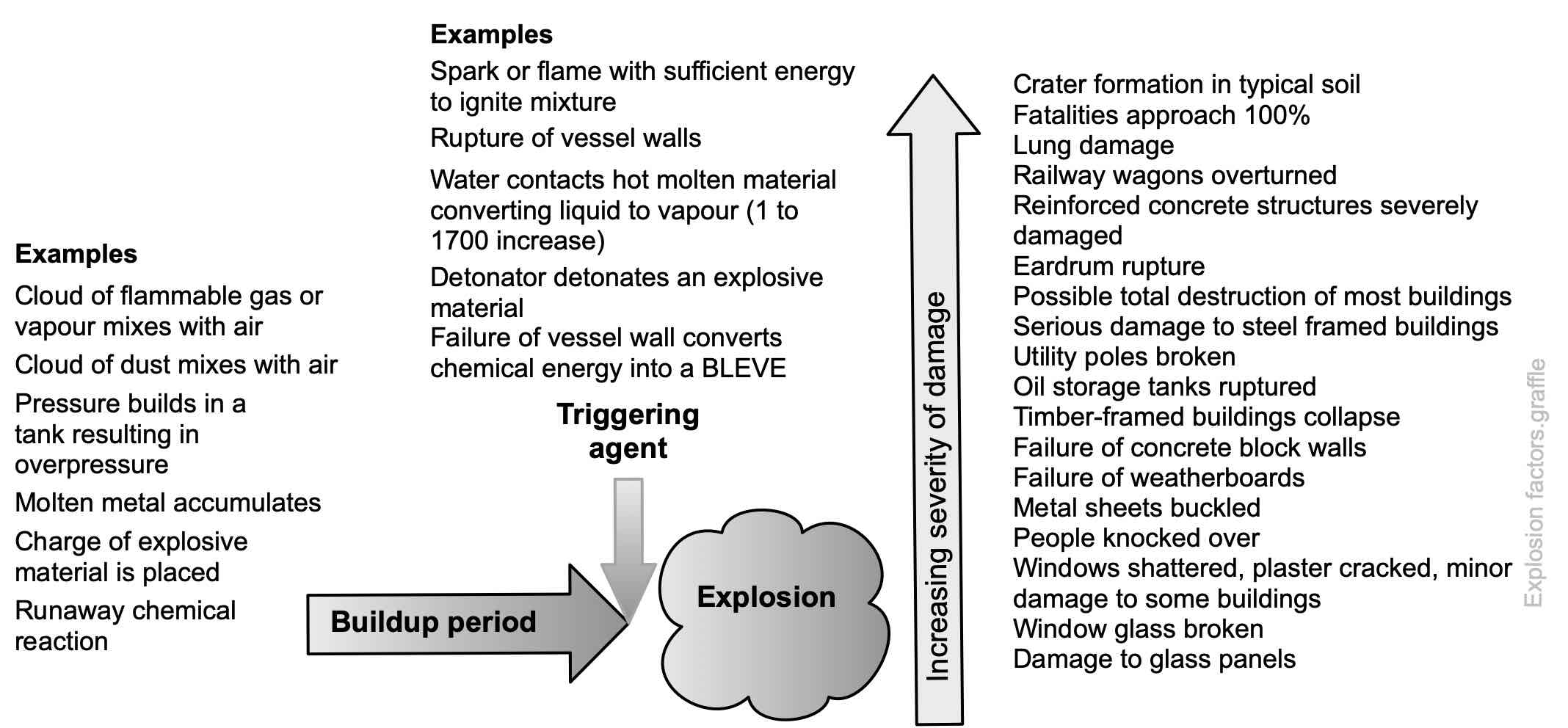
Source: Author using FM Global (2013) and Zalosh (2003)
Fuels that can result in an explosion
Dusts are an insidious cause of occupational disease and explosions in the food industry (CSB, 2008; HSE, 2007), chemicals industries (CSB, 2022a, 2022b) and production of fertiliser (Yue et al., 2023). Novel materials such as nano powders can cause explosions (Holbrow et al., 2010). See the combustible dusts website (http://go.dustsafetyscience.com/) for some information. Leaks of flammable gases and vapours can accumulate in buildings and semi-enclosed areas (Atkinson et al., 2017; BMIIB, 2008) after escaping from storage tanks (Chang & Lin, 2006). Unconfined vapour cloud explosions (UVCE) are infrequent but can cause substantial damage and harm (Bubbico et al., 2000; Landucci et al., 2011). Other explosive fuels include:
- Aluminium powder
- Bitumen emulsion
- Corn starch
- Coal dust
- Epoxy resin
- Fertiliser
- Fructose powder
- Methane
- Milk powder
- Paper tissue dust
- Rubber powder
- Sugar
- Wood dust
- Zinc powder
Explosion prevention
Explosion prevention requires a safety management system that strictly applies the hierarchy of control to eliminate or minimise the causal factors specific to the activity and the potential consequences of an explosion.
Cases of interest
Metal recycler National Steel Ltd was fined $23,500 after an explosion on 17 July 2013 revealed a catalogue of health and safety failings (WorkSafe NZ v National Steel Ltd, 2015). The explosion dislodged a long, heavy piece of metal ducting causing it to fall to the floor of the plant. Fire and the force of the explosion also damaged windows, cladding and machinery.
Mixing incompatible substances can result in an explosion as shown in 2019 at AB Specialty Silicones facility in Illinois (CSB, 2021a, 2021b). Operators were performing a batch operation that involved manually adding and mixing chemicals in a tank inside the production building. During the operation, an operator pumped an incorrect chemical into the tank, which was incompatible with another chemical that was added to the tank. The incorrect, incompatible chemical was stored in an identical drum to one of the correct chemicals, the only differentiating markings being small labels on the drums, and bung caps. After the incompatible chemicals were mixed, the tank contents underwent a chemical reaction, causing the tank contents to foam and overflow and forming a fog and hydrogen gas that exploded.
The fuel tank in a tourist launch had not been emptied before a welding operation (Maritime NZ v Kent Leppien, 2016). The welder was in the hold working on the hatch while another man was acting as spotter above. The welder accidentally pierced the fuel tank which exploded, knocking him backwards and causing minor injuries. The spotter was knocked over and suffered a badly broken ankle. The business did not provide adequate training and supervision for the welding job.
The owner of an oil recycling company was sentenced to home detention after a contract worker was killed in a tank explosion (WorkSafe NZ v Salters Cartage Ltd, 2017). The worker was carrying out ‘hot work’ on the top of a 96,000-litre capacity tank which was close to empty. The tank exploded throwing Mr Bowring 130 metres into a nearby car yard and killing him. The PCBU was fined a total of $258,750 and the business owner personally fined $25,000. The contractor who employed the worker was convicted and discharged without penalty.
“Huge gas blast kills Belgians At least 14 people were killed and 200 injured when a huge explosion tore through a gas pipeline near an industrial zone in southern Belgium yesterday, officials said. The blast near the town of Ath, 40 kilometres southwest of Brussels, sent balls of fire leaping into the sky and threw bodies hundreds of metres. Officials said the death toll could rise as many of the injured were severely wounded.
“The blast ripped through a section of the underground line carrying gas from the Belgian port of Zeebrugge to northern France as repairmen were working to plug a leak. It destroyed two nearby factories.” (Reuters Staff, 2004)
15.8 Identification of causal factors of mechanical and machinery harm
15.8.1 Mind map based on part of obsolete BS5304
The following mind map is a high-level classification of mechanical and machinery hazards. See also an extract from the long-obsolete but usefully simple BS5304 (1975) and MacDonald (2004).
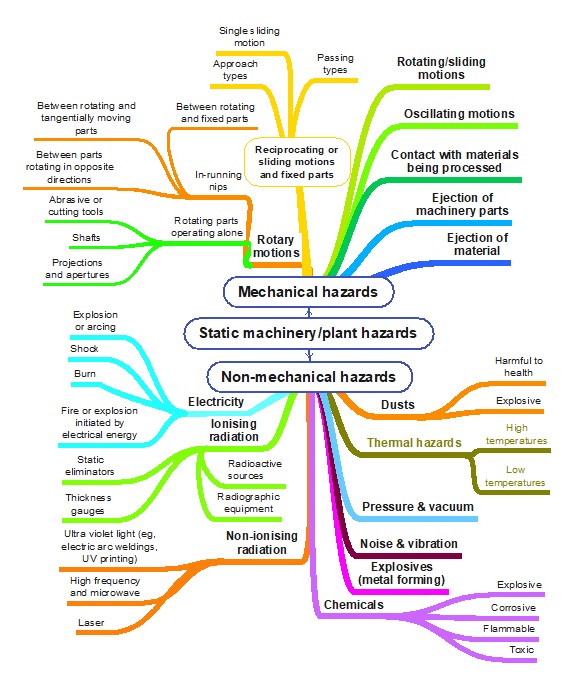
The British HSE has published many research reports of relevance, including operator visibility from a large rigid frame dumper truck (Ferreira et al., 2020a), operator visibility from a hydraulic excavator (Ferreira et al., 2020b), operator visibility from earth-moving machinery (Ferreira et al., 2020c), inadvertent operation of controls in excavator plant (Fox, 2014), the arm-locking systems of two-post vehicle lifts (Woody & McDonald, 2015).
15.8.2 Guarding machines and plant: AS/NZS4024 Safety of machinery series
A cursory reading of the following table shows that machinery safety is a specialised topic – a paper in its own right! This information is not explored further in this paper but Figure 50, the mind map above, provides some help identify possible machinery or mechanical hazards.
Table 20. Selected standards on safety of machinery
AS/NZS4024 Part number | ISO or IEC number | AS/NZS title |
1100 | Application guide. This standard was prepared by the Joint Standards Australia/Standards New Zealand Committee SF – 041, to provide background information and an application guide for the series. | |
1201 | ISO 12100-1: 2010 | General principles for design – Risk assessment and risk reduction |
1302 | Risk assessment – reduction of risks to health from hazardous substances emitted by machinery – principles and specifications for machinery manufacturers | |
1303 | ISO/TR 14121-2:2012 | Risk assessment – practical guidance and examples of methods |
1401 | Ergonomic principles – design principles – terminology and general principles | |
1501 | ISO 13840-1:1999 | Design of safety related parts of control systems – general principles for design |
1502 | ISO 13840-2:1999 | Design of safety related parts of control systems – validation |
1503 | ISO 13840-1:2006 | Safety related parts of control systems – general principles for design |
1601 | Design of controls, interlocks and guarding – guards – general requirements for the design and construction of fixed and movable guards | |
1602 | ISO 14119:2013 | Interlocking devices associated with guards – principles for design and selection |
1603 | ISO 14118 | Design of controls, interlocks, and guards – prevention of unexpected start-up |
1604 | ISO 13850:2006 | Design of controls, interlocks and guarding – emergency stop – principles for design |
1701 | ISO 7250-1:2008 | Human body measurements – basic human body measurements for technological design |
1702 | Human body measurements – principles for determining the dimensions required for whole body access into machinery | |
1703 | Human body measurements – principles for determining the dimensions required for access openings | |
1704 | Human body measurements – anthropometric data | |
1801 | ISO 13857:2008 | Safety distances to prevent danger zones being reached by upper and lower limbs |
1803 | ISO 13854:1996 | Safety distances and safety gaps – minimum gaps to prevent crushing of parts of the human body |
1901 | Displays, controls, actuators and signals – ergonomic requirements for the design of displays and control actuators – general principles for human interactions with displays | |
1902 | Displays, controls, actuators and signals – economic requirements for the design of displays and control actuators – displays | |
1903 | Displays, controls, actuators and signals – Ergonomic requirements for the design of displays and control actuators – control actuators | |
1904 | IEC 61310-1, Ed 2.0:2007 | Displays, controls, actuators and signals – Indication, marking and actuation – requirements for visual auditory and tactile signals |
1905 | IEC 61310-2, Ed 2.0 2007 | Displays, controls, actuators and signals –Indication, marking and actuation – requirements for marking |
1906 | IEC 61310-3, Ed 3.0:2007 | Displays, controls, actuators and signals –System of auditory and visual danger and information signals |
15.9 Naming the effects of uncertainty on objectives
Risks should be named in a consistent manner to state:
- a source of uncertainty
- a cause or causes arising from that source
- an event or changes in specific circumstances it caused
- the consequences that could flow from the event
- the effect(s) on objectives.
Note that an event can include a change in specific circumstances.
How much uncertainty, how many effects on objectives, types, or sources of uncertainty?
All significant causes and consequences should be considered. See ISO31000 (2018) clause 6.4.2 for a list of factors. What does “significant” mean? The opposite might be “trivial”, and you may have to work through risk naming, analysis, and evaluation and back to risk identification several times before being satisfied that the currently significant causes of uncertainty and their effects have been identified.
Remember also that risks that are currently significant can change if the context changes. This emphasises the need to make risk assessment a truly dynamic part of the overall risk management process, revised and repeated after a significant change in the context of a business or undertaking.
Types of uncertainty or sources of uncertainty?
Often risks are classified as strategic, occupational health and safety, financial, and so on. However, this can be misleading because strategic risks, for example, may be given so much attention that they cease to be significant. Conversely, a safety-related or project-related risk may seem operational and low level yet be capable of causing severe harm to the organisation. Table 21 (adapted from Kaplan & Mikes, 2012) suggests how risks can be classified for:
- strategy- or project-related sources of risk (eg, as managed through clause 6, ISO45001)
- business-as-usual sources of risk (eg, as managed in clause 8, ISO45001)
- external sources of causes that may be uncontrollable (eg, as managed through clause 8, ISO22301 (2019) and other management system standards).
Note that business-as-usual risks can become strategy-related and, for some organisations, (eg, civil defence, Fire and Emergency NZ, ambulance service) external, “uncontrollable” sources are business-as-usual.
Table 21. Three sources of uncertainty
Clause 6 ISO45001 and other management system standards Strategy-related sources |
Clause 8 ISO45001 and other management system standards Business-as-usual sources |
Clause 8 ISO22301 and other management system standards External, “uncontrollable” sources |
|
Explanation | Uncertainty and effects accepted for superior strategic or long-term returns or for major changes to systems, services, products, etc | Uncertainty and effects arising within the organisation that usually generate no strategic benefits | Uncertainty and effects with causes outside the control of the organisation but whose consequences are, to some extent, controllable by the organisation |
Examples | Innovative products or processes; major change from established services; responses to shifts in market preferences | Unauthorised, illegal, unethical, incorrect, or inappropriate actions; breakdowns in routine operational processes; regulatory non-compliance | Major natural hazards; major financial failures in an economy or region; new or disruptive technology or competitor |
Examples of controls | Modify uncertainty and effects cost-effectively to: • reduce negative consequences or their probability or both • increase positive consequences or their probability or both |
Modify uncertainty and effects cost-effectively to: • reduce negative consequences or their probability or both • increase positive consequences or their probability or both |
Modify vulnerable assets
Develop contingency plans to enable a timely response, eg: |
All three may give rise to disruption of business objectives and therefore contingency plans should cover all. | |||
Control model | Interactive discussions about uncertainty and effects to strategic objectives and long-term plans drawing on tools such as: • scenario planning (5-, 10- or 15-year horizon) • key risk indicators |
Integrated culture-and-compliance model
Develop mission statement; values and beliefs systems; rules and boundary systems; standard operating procedures; internal controls; and internal audit |
Envisioning uncertainty and effects through: • scenario planning (5-, 10- or 15-year horizon) • long tail assessments and stress testing • war gaming |
Role of management specialists | Convene a board of technical experts to challenge assumptions
Facilitate workshops to assess and review uncertainty and effects on objectives Help develop treatment plans including finance (eg, insurance) Embedded experts, act as devil’s advocate |
Collaborate with internal audit to coordinate, oversee, and revise specific controls | Run stress-testing, scenario-planning, and war-gaming exercises with the management team
Act as devil’s advocate |
Monitoring and review activities | Review long-term projects to ensure they remain relevant
Challenge assumptions |
Internal audits across systems
Third party reviews Reengineer or lean review to re-align system controls with changes in context |
Monitor and review changes in context and long-term trends to identify opportunities and threats (eg, changes in demographics, climate, consumer demand, technology, etc) |
Governance reporting | Overview of changes to reasons for major projects
Changes since last report; changes happening; possible or anticipated changes |
Overview of business-as-usual uncertainties in and to systems; include summary of control effectiveness and progress with treatments
Changes since last report; changes happening; possible or anticipated changes |
Results of tests of contingency plans
Changes in response capabilities since last report Capability trends in last XX months or years |
15.10 Chapter summary
This chapter has covered identification of some sources of harm to people, including human and performance-shaping factors, causes of occupational ill-health, and machinery. The next chapter sets out a process to analyse these sources and how uncertainty can affect objectives.
15.11 References used in this chapter
Aneziris, O. N., Papazoglou, I. A., Baksteen, H., et al. (2008). Quantified risk assessment for fall from height. Safety science, 46(2), 198-220. https://doi.org/10.1016/j.ssci.2007.06.034
Atkinson, G., Hall, J., & McGillivray, A. (2017). Review of vapour cloud explosion incidents [Research Report RR1113]. Health and Safety Executive, Buxton. https://www.hse.gov.uk/research/publish.htm
Bailey, C., Brookes, J., & Evans, G. (2022). Metalworking fluid and use of compressed airguns in machining: expert workshop [Research Report RR1171]. Health and Safety Executive, Buxton. https://www.hse.gov.uk/research/publish.htm
Bates, S., & Holroyd, J. (2012). Human factors that lead to non-compliance with standard operating procedures [Research Report RR0919]. Health and Safety Executive, Buxton. https://www.hse.gov.uk/research/publish.htm
Beards, P., Cope, M., & Longden, S. (2018). Common human factors underlying worker fatalities in the waste and recycling industry [Research Report RR1128]. Health and Safety Executive, Buxton. https://www.hse.gov.uk/research/publish.htm
Bellamy, L., & Geyer, T. (2007). Development of a working model of how human factors, safety management systems and wider organisational issues fit together [Research Report RR00543]. Health and Safety Executive, Buxton. https://www.hse.gov.uk/research/publish.htm
Benke, G., & Cross, M. (2019). Occupational health, basic toxicology and epidemiology. In S. Reed, D. Pisaniello, & G. Benke (Eds.), Principles of occupational health & hygiene: an introduction (3rd ed., pp. 27-51). Allen & Unwin.
BMIIB. (2008). The Buncefield Incident 11 December 2005: The final report of the Major Incident Investigation Board [Incident Investigation report]. Buncefield Major Incident Investigation Board, London. http://www.hse.gov.uk/comah/investigation-reports.htm
BS5304: 1975 Code of practice: safeguarding of machinery, British Standards institution, London.
BSRIA Ltd. (2006). A literature review of the effects of environment microclimatic conditions on the slip potential for flooring [Research Report RR0471]. Health and Safety Executive, Buxton. https://www.hse.gov.uk/research/publish.htm
Bubbico, R., Ferrari, C., & Mazzarotta, B. (2000). Risk analysis of LPG transport by road and rail. Journal of Loss Prevention in the Process Industries, 13(1), 27-31. https://doi.org/10.1016/s0950-4230(99)00057-1
Chang, J. I., & Lin, C.-C. (2006). A study of storage tank accidents. Journal of Loss Prevention in the Process Industries, 19(1), 51-59. https://doi.org/DOI: 10.1016/j.jlp.2005.05.015
Cherrie, J. W. (2023). Occupational exposure science. Annals of Work Exposures and Health, wxad052. https://doi.org/10.1093/annweh/wxad052
Cockayne, S., Fairhurst, C., Frost, G., et al. (2021). Slip-resistant footwear reduces slips among National Health Service workers in England: a randomised controlled trial. Occupational and Environmental Medicine, 78(7), 472. https://doi.org/10.1136/oemed-2020-106914
CSB. (2008). Sugar Dust Explosion and Fire: Imperial Sugar Company [Incident Investigation report 2008-05-I-GA]. Chemical Safety and Hazard Investigation Board, Washington, DC. http://www.csb.gov/
CSB. (2021a). Chemical Reaction, Hydrogen Release, Explosion, and Fire at AB Specialty Silicones [Incident Investigation report 2019-03-I-lL]. Chemical Safety and Hazard Investigation Board, Washington, DC. http://www.csb.gov/
CSB. (2021b). Chemical Reaction, Hydrogen Release, Explosion, and Fire at AB Specialty Silicones [Video]. Chemical Safety and Hazard Investigation Board. http://www.csb.gov/
CSB. (2022a). Flash Fire and Explosion at Sunoco Partners Nederland Terminal [Incident Investigation report 2016-03-I-TX]. Chemical Safety and Hazard Investigation Board, Washington, DC. http://www.csb.gov/
CSB. (2022b). Pressure Vessel Explosion at Loy-Lange Box Company [Incident Investigation report 2017-04-I-MO]. Chemical Safety and Hazard Investigation Board, Washington, DC. http://www.csb.gov/
Darby, A. (2012). Optimisation of the mechanical slip resistance test for footwear used in EN ISO 13287:2007: Follow on study [Research Report RR0951]. Health and Safety Executive, Buxton. https://www.hse.gov.uk/research/publish.htm
Dekker, S. (2014). The Field Guide to Understanding ‘Human Error’ (3rd ed.). Ashgate Publishing Ltd.
Ferreira, J., Riley, D., & Grimes, A. (2020a). Application of a risk-based method to evaluate operator visibility from a large rigid frame dumper truck [Research Report RR1158]. Health and Safety Executive, Buxton. https://www.hse.gov.uk/research/publish.htm
Ferreira, J., Riley, D., & Grimes, A. (2020b). Application of a risk-based method to evaluate operator visibility from an hydraulic excavator [Research Report RR1157]. Health and Safety Executive, Buxton. https://www.hse.gov.uk/research/publish.htm
Ferreira, J., Riley, D., & Grimes, A. (2020c). Visibility risk zone method to evaluate operator visibility for earth-moving machinery [Research Report RR1156]. Health and Safety Executive, Buxton. https://www.hse.gov.uk/research/publish.htm
FM Global. (2002). Boiler furnace implosions [Property Loss Prevention Data Sheet 6-6]. Author, Johnston, RI. http://www.fmglobal.com
FM Global. (2013). Causes and effects of fires and explosions [Property Loss Prevention Data Sheet 7-0]. Author, Johnston, RI. http://www.fmglobal.com
Fox, D. (2010). Footwear and modifications to goods vehicles in the UK road haulage sector: A survey of goods vehicle drivers [Research Report RR0793]. Health and Safety Executive, Buxton. https://www.hse.gov.uk/research/publish.htm
Fox, D. (2014). Inadvertent operation of controls in excavator plant – insight, analysis and recommendations for prevention by design [Research Report RR1000]. Health and Safety Executive, Buxton. https://www.hse.gov.uk/research/publish.htm
Fox, D., Harding, A.-H., & Frost, G. (2017). Occupational health and extended working lives in the transport sector [Research Report RR1104]. Health and Safety Executive, Buxton. https://www.hse.gov.uk/research/publish.htm
Frost, G., Liddle, M., Cockayne, S., et al. (2022). Relationship between age, workplace slips and the effectiveness of slip-resistant footwear among healthcare workers. Injury Prevention, 28(3), 256. https://doi.org/10.1136/injuryprev-2022-044533
Gervais, R., & McCann, P. (2013). Access equipment for construction work at height in residential properties [Research Report RR0978]. Health and Safety Executive, Buxton. https://www.hse.gov.uk/research/publish.htm
Gollan, L. (2022). Occupier liable for slip on stairs not compliant with the Australian Building Code. Lexology. Retrieved 30 September from https://www.lexology.com/
Hall, S., Pengelly, I., Staff, J., et al. (2019). Measuring and controlling emissions from polymer filament desktop 3D printers [Research Report RR1146]. Health and Safety Executive, Buxton. https://www.hse.gov.uk/research/publish.htm
Hallas, K., & Shaw, R. (2005). The Efficacy of Cleaning Regimes [Research Report HSL/2005/26]. Health and Safety Executive, Sheffield. https://www.hse.gov.uk/research/hsl/
Hodge, K., & Bowler, S. (2023). It Is a Cultural Thing: Can Employers Be Held Liable for a Poor Workplace Culture? Lexology. https://www.lexology.com/
Hoey, V. (2017). Track occupation irregularity, leading to near collision, Between Manunui and Taumarunui, 15 December 2015 [Investigation Report RO-2015-103]. Transport Accident Investigation Commission, Wellington. https://www.taic.org.nz/
Holbrow, P., Wall, M., Sanderson, E., et al. (2010). Fire and explosion properties of nanopowders [Research Report RR0782]. Health and Safety Executive, Buxton. https://www.hse.gov.uk/research/publish.htm
Houlihan, R., Mole, M., & Lemon, P. (2009). A further study of the influence of dry contaminants on pedestrian slips [Research Report RR0753]. Health and Safety Executive, Buxton. https://www.hse.gov.uk/research/publish.htm
HSE. (1999). Reducing error and influencing behaviour [Guidance Note HS(G) 48]. HSE Books,, Sudbury. http://www.hse.gov.uk/
HSE. (2007). Prevention of dust explosions in the food industry. HSE. Retrieved 14 September 2007 from https://www.hse.gov.uk/food/dustexplosion.htm
HSE. (2022). Fire safety in construction [Guidance Note: General Series HSG168]. The Stationery Office, https://www.hse.gov.uk/pubns
HSWGR (2016), Health and Safety at Work (General Risk and Workplace Management) Regulations. New Zealand. http://www.legislation.govt.nz/
Hunwin, G. (2012). Suitability of Slider 55 rubber for use as a standardised slider material for the simulation of barefoot pedestrians [Research Report RR0940]. Health and Safety Executive, Buxton. https://www.hse.gov.uk/research/publish.htm
IEC62508: 2015 Human aspects of dependability, International Electrotechnical Commission, Geneva.
ISO22301: 2019 Societal security – Business continuity management systems – Requirements, International Standards Organization, Geneva.
ISO31000: 2018 Risk management – Guidelines, International Standards Organization, Geneva.
ISO31073: 2022 Risk management — Vocabulary, International Standards Organization, Geneva.
Kaplan, R. S., & Mikes, A. (2012). Managing risks: a new framework. Harvard Business Review, 90(6), 48-60.
Kjellstrom, T., Freyberg, C., Lemke, B., et al. (2018). Estimating population heat exposure and impacts on working people in conjunction with climate change. International journal of biometeorology, 62(3), 291-306. https://doi.org/10.1007/s00484-017-1407-0
Kool, B. (2001). Work-related Fatal and Non-fatal Fire Injuries in New Zealand 1985-1999 [Research Report 65]. NZ Fire Service Commission, Wellington. https://www.fireandemergency.nz/research-and-reports/research-reports/
Landucci, G., Tugnoli, A., Busini, V., et al. (2011). The Viareggio LPG accident: Lessons learnt. Journal of Loss Prevention in the Process Industries, 24(4), 466-476. https://doi.org/10.1016/j.jlp.2011.04.001
Liddle, M. (2009). Assessment of slips safety information/ literature provided by flooring and footwear suppliers [Research Report RR0747]. Health and Safety Executive, Buxton. https://www.hse.gov.uk/research/publish.htm
Loo-Morrey, M. (2006). A study of the slip characteristics of applied epoxy resin flooring and thin coat epoxy base materials [Research Report RR0497]. Health and Safety Executive, Buxton. https://www.hse.gov.uk/research/publish.htm
Loo-Morrey, M. (2007). Ramp testing pre-engineered wood floors [Research Report RR0533]. Health and Safety Executive, Buxton. https://www.hse.gov.uk/research/publish.htm
Loo-Morrey, M., & Lemon, P. (2007). A study of the slip characteristics of metal flooring materials [Research Report RR0534]. Health and Safety Executive, Buxton. https://www.hse.gov.uk/research/publish.htm
Macdonald, D. W. (2004). Risk assessment and risk reduction. In D. M. Macdonald & S. Mackay (Eds.), Practical Machinery Safety (pp. 56-91). Newnes. https://doi.org/10.1016/B978-075066270-3/50003-1
Maritime NZ v Kent Leppien [2016] Nelson District Court.
Mason, S. (2003). Development of a methodology for the assessment of human factors issues relative to trips, slips and fall accidents in the offshore industries [Research Report RR0065]. Health and Safety Executive, Buxton. https://www.hse.gov.uk/research/publish.htm
Miller, G. (1994). The Magical Number Seven, Plus or Minus Two: Some Limits on Our Capacity for Processing Information. Psychological Review, 101(2), 343-352. http://www.musanim.com/miller1956/
Munkman, J. (1975). Employer’s liability at common law (8th ed.). Butterworths.
Peebles, L., Wearing, S., & Heasman, T. (2005). Identifying human factors associated with slip and trip accidents [Research Report RR0382]. Health and Safety Executive, Buxton. https://www.hse.gov.uk/research/publish.htm
Perrow, C. (1999). Normal Accidents: living with high-risk technologies. Princeton University Press.
Pinder, A., & Okunribido, O. (2019). Comparative analysis of manual handling practices in kerbside collection of recyclable waste [Research Report RR1141]. Health and Safety Executive, Buxton. https://www.hse.gov.uk/research/publish.htm
Rasmussen, J. (1997, 1997/11/01/). Risk management in a dynamic society: a modelling problem. Safety Science, 27(2), 183-213. https://doi.org/10.1016/S0925-7535(97)00052-0
Reason, J. (1990). Human Error. Cambridge University Press.
Reason, J. (1998). Achieving a safe culture: Theory and practice. Work & Stress, 12(3), 293-306. https://doi.org/10.1080/02678379808256868
Reuters Staff. (2004, 31 July). Huge gas blast kills Belgians. Dominion.
Safe Work Australia. (2022). Managing psychosocial hazards at work [Code of Practice]. Author, Canberra. https://www.safework.nsw.gov.au/
Scott, A. (2004). Analysis of Slips, Trips and Falls in the UK Printing and Publishing Industries, 2002-2003 [Research Report PED/04/09]. Health and Safety Laboratory, Buxton. https://www.hse.gov.uk/research/rrhtm/index.htm
Scott, A. (2005). Falls on Stairways – Literature Review [Research Report HSL/2005/10]. Health and Safety Laboratory, Buxton. https://www.hse.gov.uk/research/publish.htm
Scott, A., Miller, M., & Hallas, K. (2006). The underlying causes of falls from vehicles associated with slip and trip hazards on steps and floors [Research Report RR0437]. Health and Safety Executive, Buxton. https://www.hse.gov.uk/research/publish.htm
Shaw, R. (2007a). An examination of novel roughness parameters to be used in conjunction with the HSE slips assessment tool (SAT) [Research Report RR0549]. Health and Safety Executive, Buxton. https://www.hse.gov.uk/research/publish.htm
Shaw, R. (2007b). A study of the characteristics of cementitious surface toppings and applied concrete [Research Report RR0547]. Health and Safety Executive, Buxton. https://www.hse.gov.uk/research/publish.htm
Shaw, R., Lemon, P., & Thorpe, S. (2009). Development of a more accurate assessment of roughness parameters for flooring [Research Report RR0732]. Health and Safety Executive, Buxton. https://www.hse.gov.uk/research/publish.htm
Sheedy, E., Zhang, L., & Tam, K. (2017). Are profit-based incentives compatible with a risk culture? MacQuarie University, Sydney. www.mafc.mq.edu.au
Simon, H. A. (1979). Rational Decision Making in Business Organization. American Economic Review, 69(4), 493-513.
Smith, D. (2011). Reliability, maintainability and risk: Practical methods for engineers (8th ed.). Butterworth-Heinemann.
Spearpoint, M., & Hopkin, C. (2020). A model for the evaluation of fatality likelihood associated with falls from heights. Fire safety journal, 112. https://doi.org/10.1016/j.firesaf.2020.102973
Tanvi Newaz, M., Ershadi, M., Carothers, L., et al. (2022, 2022/03/01/). A review and assessment of technologies for addressing the risk of falling from height on construction sites. Safety Science, 147, 105618. https://doi.org/10.1016/j.ssci.2021.105618
Tappin, D., Bentley, T., & Legg, S. (2004). An exploratory analysis of falls in New Zealand small business residential construction. The Journal of occupational health and safety, Australia and New Zealand, 20(6), 539.
Turner, B. (1978). Man-made disasters. Wykeham Publications.
Williams, J. C. (1985). Validation of human reliability assessment techniques. Reliability Engineering, 11(3), 149-162. https://doi.org/10.1016/0143-8174(85)90068-X
Wolters Kluwer Australia. (2021). Holiday house owners liable in negligence for slip and fall off back veranda (NSW). Lexology. Retrieved 30 September 2022 from https://www.lexology.com/
Woodcock, K. (2007). Rider errors and amusement ride safety: Observation at three carnival midways. Accident Analysis and Prevention, 39, 390-397.
Woody, P., & McDonald, A. (2015). Assessment of the arm locking systems of two-post vehicle lifts [Research Report RR1030]. Health and Safety Executive, Buxton. https://www.hse.gov.uk/research/publish.htm
WorkSafe NZ v National Steel Ltd [2015] Manukau District Court.
WorkSafe NZ v Precision Animal Supplements Ltd [2018b] NZDC 19342 Ashburton District Court. https://www.districtcourts.govt.nz/
WorkSafe NZ v Salters Cartage Ltd [2017] NZDC 26277 Manukau District Court. https://www.worksafe.govt.nz/about-us/news-and-media/oil-recycler-sentenced-over/
WorkSafe NZ v Waipa Workingmen’s Club Incorporated [2016] Te Awamutu District Court.
Yoon Cheol Hong v Chevron Traffic Services Ltd [2019] Auckland Employment Court. https://www.employmentcourt.govt.nz/judgments/decisions/?Filter_Jurisdiction=17&Year=2020&Month=4&Day=15
Yue, Y., Gai, W., & Boustras, G. (2023). Exploration of the causes of ammonium nitrate explosions: Statistics and analysis of accidents over the past 100 years. Safety Science, 158, 105954. https://doi.org/10.1016/j.ssci.2022.105954
Zalosh, R. (2003). Explosions. In A. Cote, J. Hall, P. Powell, & C. Grant (Eds.), Fire Protection Handbook (19th ed.). National Fire Protection Association, Inc.
Zarei, E., Khan, F., & Abbassi, R. (2023). An advanced approach to the system safety in sociotechnical systems. Safety science, 158. https://doi.org/10.1016/j.ssci.2022.105961